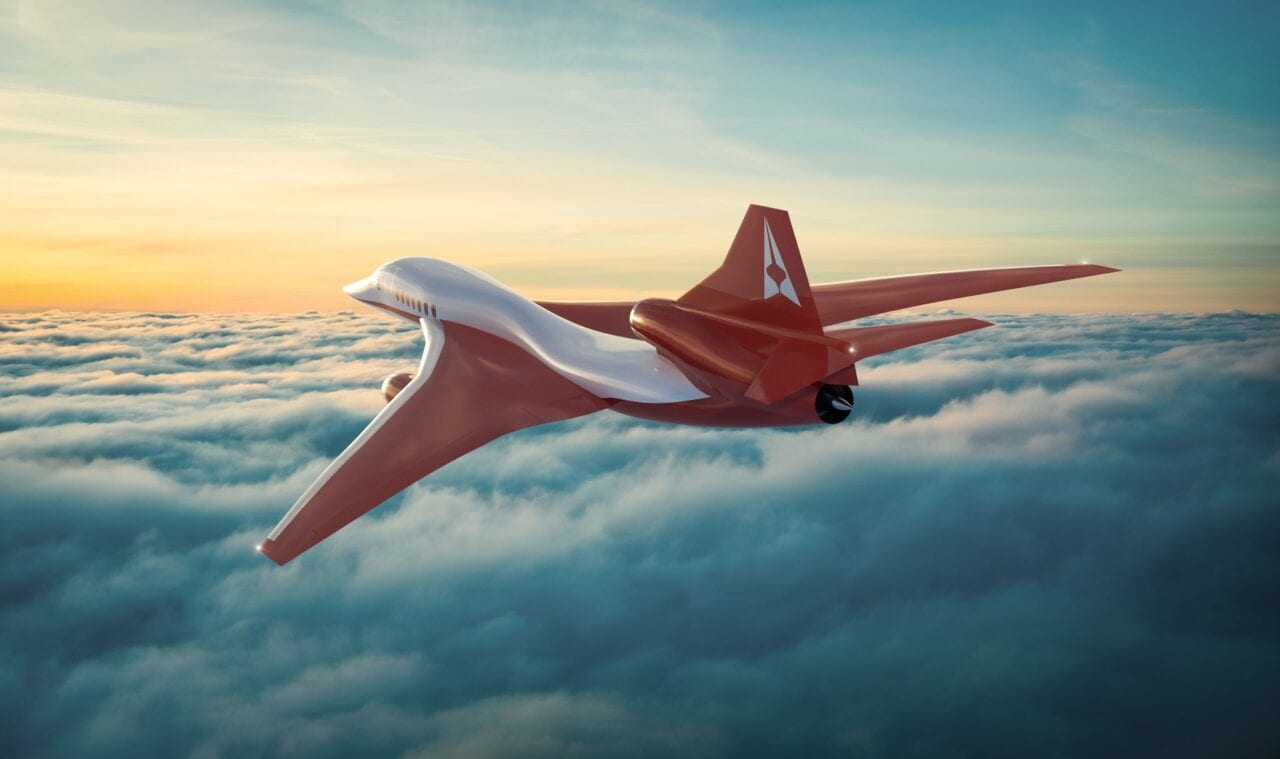
Aerion has new avionics, connectivity and flight control systems agreements and advancements with Honeywell Aerospace and BAE Systems. (Aerion)
New design progress and supplier agreements for avionics, flight controls and connectivity have the AS2 supersonic business jet on track for type certification by the mid to late 2020s, Aerion COO Steve Berroth told Aviation Today in a recent interview.
Aerion’s latest development update for its 8-10 passenger jet designed to fly at a max speed of Mach 1.4 includes achieving the joint definition phase of avionics and connectivity with Honeywell Aerospace and a supplier partnership for its fly-by-wire flight control system, including active inceptors from BAE Systems. Both agreements, announced last week, will borrow from existing and new aircraft network and pilot user interface systems such as Honeywell’s Forge data analytics platform synced with the initial design of the flight deck.
BAE Systems described the active inceptors it will supply in a Sept. 15 press release as providing pilots with both static and dynamic tactile force feedback where “the active inceptor includes electronic controlled actuators that send tactile feedback to the pilot through the flight stick. The feedback warns pilots of structural or aerodynamic operating limits,” the company said.
“Our plan is three large format, touchscreen displays and three small format iPad size displays. The goal here with Honeywell’s avionics development is to use automation and touchscreen interface control where possible to reduce the pilot’s workload. We want to achieve unsurpassed levels of situational awareness based upon our different phases of flight, transitioning from transonic to supersonic and Boomless cruise,” Berroth said.
Aerion first began working with Honeywell in 2018, three years after establishing FlexJet as the launch partner for its $120 million supersonic business jet. In a Sept. 14 press release, Aerion confirmed it has reached “the joint definition phase for avionics and connectivity,” which will keep the development of the AS2 on track to achieve type certification by 2027, Berroth said.
Berroth describes Boomless cruise as a key feature in focus for the avionics that Honeywell will supply for the aircraft. He said it is not new technology, but that the enabling systems needed to allow Boomless cruise only recently became available.
According to Berroth, the concept involves the use of a ground-based system creating an initial flight plan using a high fidelity weather model and a “trained model,” B, that is computed together to send a flight plan to the aircraft via satellite, VHF data link or a cellular network using Honeywell’s integrated network server unit (INSU).
“There will be an Aerion created application that we will be trademarking that will be hosted within the Honeywell integrated modular avionics that’ll combine the ground data and the data from multiple airborne systems to determine a valid Boomless cruise flight plan,” Berroth said.
The key to enabling the Boomless cruise flight plan will be monitoring changes in terrain and weather in near real time to ensure the impact of a supersonic boom never hits the ground when the AS2 is flying over land. Pilots will not be able to disengage the Boomless cruise functionality unless they’re flying over the ocean.
Mike Ingram, vice president and general manager of Honeywell Aerospace, said there are some details associated with the AS2’s avionics and connectivity development that they’re unable to discuss at this point.
“What you will see in the cockpit will be very new and something that hasn’t been released into the market yet,” Ingram said. “It will be a combination of customizing some of the existing Honeywell Primus Epic software, and leveraging some of the newest touchscreen interface and controller technologies. We will be able to show the best Boomless cruise path for the aircraft based on how our algorithms determine that using the latest updated flight plan information.”
Berroth echoes this sentiment, noting that his vision of the pilot’s user interface for AS2 will be a display that features a “carpet laid out in front of the pilot” showing the optimal flight path for Boomless cruise.
Another design consideration for the AS2’s connectivity system will be the development of an antenna that accommodates Aerion’s goal of reducing aerodynamic drag to achieve Mach 1.4.
“There’s multiple suppliers right now that can provide a connectivity system that meets our stringent performance requirements. There is a very large concern that they need to be conformal antennas so we reduce drag, and there is some development work that needs to go on in that area. We’re working right now with suppliers that can support that kind of design,” Berroth said.
Outside of their ongoing development work with Honeywell and BAE Systems, Aerion is also working with regulators to update regulations for flying supersonic over the continental United States. Currently, that type of flying is not permitted, however, the FAA took action toward allowing supersonic flying with a notice of proposed rulemaking published in March that updates the requirements for applicants that seek special flight authorization for flying above Mach 1 in the United States.
Aerion plans to begin production of the AS2 by 2023.