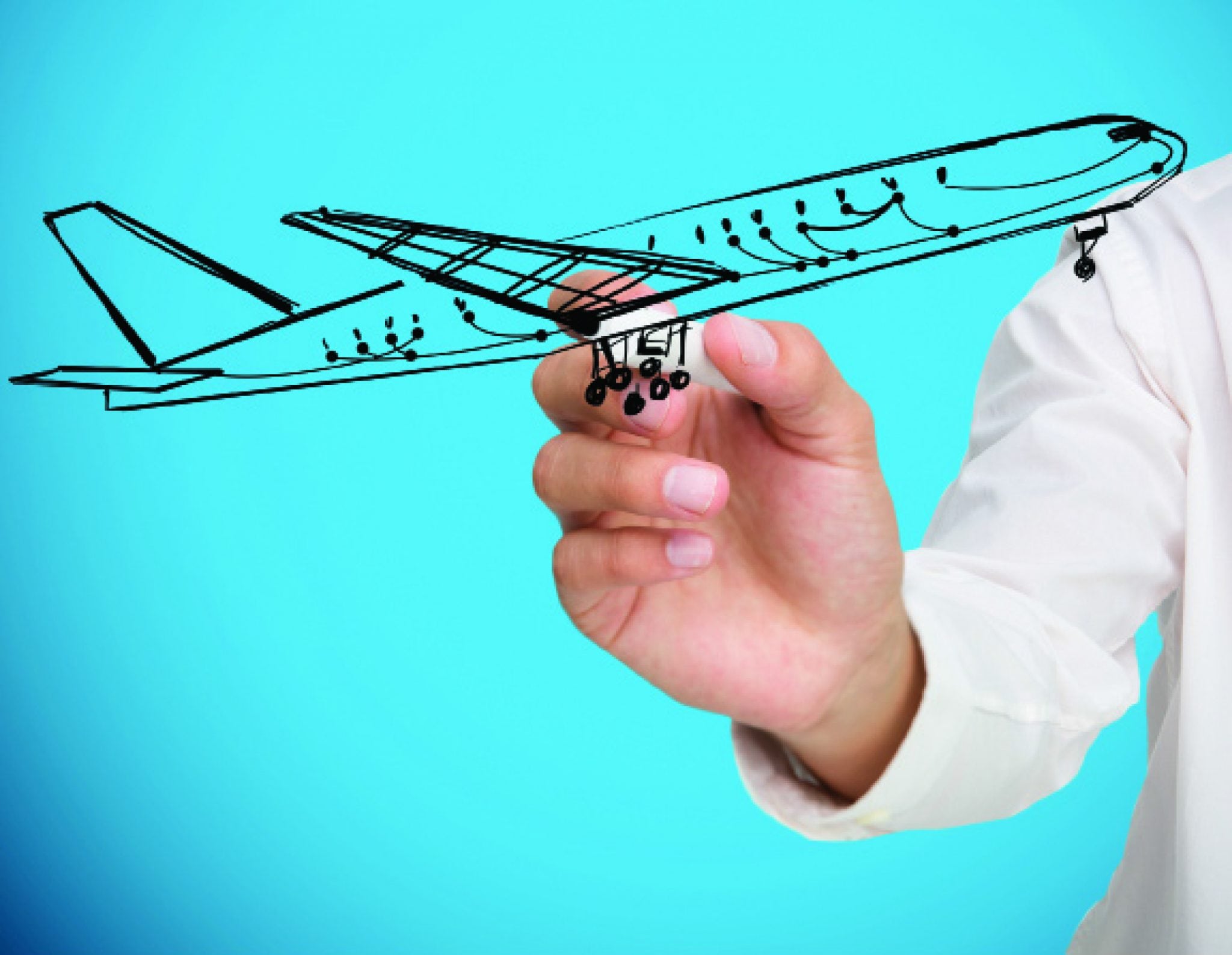
Avionics manufacturers are constantly innovating and releasing new technology to the market, from Enhanced Vision Systems (EVS) in the cockpit to next generation In-flight Entertainment (IFE) systems and on-board servers in the cabin. But what’s the key to enabling lightning-fast data transfers throughout the aircraft necessary to keep these new technologies functioning? Specialized wire and cable solutions that support data transfer rates of up to 10 GB per second. Now consider that this is occurring on today’s commercial, military and corporate aircraft at altitudes of more than 30,000 feet, sometimes in remote airspace where bandwidth availability is limited for functions such as passengers connecting to in-flight Wi-Fi systems.
Wire and cables are also becoming ever more critical in the data-centric architecture of modern aircraft. For example, when developing the 787, Boeing selected lighter weight, more efficient solutions, managing to cut the length of wiring to between 60 and 70 miles — about 25 miles less than the 767. Even those aircraft wire and cables that were placed on 787s when it first entered service will eventually become outdated as Boeing works with suppliers to improve its flagship aircraft. And a lot of general aviation and commercial air transport jets that are still in service today need wire and cable upgrades. As an example, more than 80 percent of Avionics Magazine readers who responded to our Wire & Cable Survey said that they need wire and cable upgrades, retrofits, line fits and maintenance.
Commercial
For most of the industry’s major aerospace wire and cable companies, commercial aircraft production volumes are driving demand. Our Avionics magazine survey results also reflected this need for commercial wire and cable solutions, with 38 percent of readers reporting wire and cable needs pertaining to commercial airframes. General aviation and military aircraft operators ranked second and third in the survey, while the majority of business aviation operators are satisfied with their current setup, as only 11 percent of our readers say they want to re-wire their corporate aircraft.
According to Don Slutz, senior product manager for digital solutions at Carlisle Interconnect Technologies (CarlisleIT), the highest demand from the commercial market is for Ethernet cables that are capable of data transfer rates of 1 GB per second because of “the increasing communication speeds we’re required to support and higher speed applications.”
“In the last two years, the data rate requirements have exponentially increased going from a typical 100BasedT to 10G requirement. More sophisticated avionics, increased data processing requirement, higher resolution displays and the expansion of IFE are driving these needs,” Slutz says.
Currently, CarlisleIT’s most robust product offering is its Gigabit 10HP, which features a bonded pair design to provide 10 GB performance over distances of up to 295 feet, according to John Dunn, technical director of wire and cable at CarlisleIT. According to Dunn, this is the type of cable that is capable of handling higher resolution cockpit displays and the expansion of IFE options being deployed on today’s bandwidth- and data-hungry aircraft.
Other long running aerospace wire and cable manufacturers, such as TE Connectivity, are also seeing increased demand, with a concentration in IFE systems on commercial aircraft, says Robert Moore, principal engineer and high speed specialist of TE Connectivity’s aerospace and defense manufacturing wire and cable division. Airlines such as Southwest, JetBlue and Emirates, among others, feature IFE setups that feed Ethernet wire and cable connections from on-board servers to seats all filled with wire and cables. These cables are of course hidden to the passenger who only sees seat cushions and trays.
“Movie choices, television program choices, music and games, that’s all coming off of a server and an aircraft can have 300 or more passengers trying to get data off that … there’s a lot of data that’s moving around,” says Moore.
Adding connectivity to that original IFE on-board server-to-seat setup has created another market for wire and cable solutions as well.
“You look at what the airlines have also done, is to add Wi-Fi Internet access onto the aircraft. That’s another area where the wireless antennas are going back to the avionics and getting that signal out of the aircraft. You’re talking either gigabit or 10 gigabit Ethernet in those systems, I think right now they’re typically gigabit,” said Moore.
Aircraft engines heavily influence demand for wire that can perform at high operating temperatures. SEA Wire and Cable, a U.S.-based distributor supply chain manager of wire and cable, partnered with its top supplier, Berkshire Hathaway subsidiary RSCC Aerospace, to release a new aerospace wire that targets the needs of connecting the aircraft engine to the flight management system, data buses and other data acquisition systems.
“We’re introducing a beta version to the market right now, we’re looking at some aircraft use in some engines because we have a 300-degrees Celsius version of it as well. The spec name on it would be the AD-150, 200, 260 and 300 all dealing with the temperature supported,” said Jim Duggan, director of sales and marketing at SEA Wire and Cable.
Between the 2013 Dubai Airshow and the 2014 Farnborough Airshow, the world’s largest airlines spent nearly $300 billion on new commercial airframes. Following Farnborough, Airbus and Boeing have received more than 1,300 orders combined for commercial aircraft. This trend in demand is expected to continue. Both companies project demand to increase in the future, spurred by increased popularity in passenger travel in the Asia-Pacific market.
With modern aircraft featuring anywhere from 70 to 300 miles of wire on average — the Airbus A380 features an estimated 328 miles while the Boeing 787 features just 60 — that’s enough to keep the wire and cable market lucrative for the next two decades. Even if new production airframe programs continue to look to cut miles of wire in order to reduce weight as fuel efficiency continues to be the focus at the primes.
Military
While defense spending is down in the United States and Europe, there is still a demand in the military market for modernized wire and cable solutions. This is because the top-featured military fighter jets across the globe are F-16 and F-18 legacy fighter jets, many of which were introduced into service in the 1980s and 90s. Rather than the billion-dollar fleet overhauls that commercial airlines are pulling off right now, decision-makers in the military are favoring Service Life Extension Programs (SLEP). While there definitely is still demand for new wire and cable installations for air defense programs, our survey results show the stark contrast between the military and commercial markets. Only 22 percent of respondents say that SLEP programs are the most compelling reason to purchase aircraft wires and/or cables.
There are a number of key trends at work in the military market. We are seeing newer processors, more advanced jam-resistant radar systems and the elimination of stove pipe buttons flight decks for surveillance screens. High definition cockpit displays with synthetic vision are being inserted into both fixed wing and rotary wing aircraft for military air defense programs across the globe. Every time a government outsources an avionics overhaul program to a third-party team, it requires extensive re-wiring and the installation of Ethernet cables to handle the data-centric architecture of fourth and fifth generation jets.
Seamless T is CarlisleIT’s latest composite aerospace wire. Featured on the F-35, the Seamless T is AS22759/180-192 that serves as a general-purpose hookup wire for power distribution and signal applications across multi-conductor aircraft cables. It is currently featured on the F-35, Lockheed Martin’s fifth-generation network-centric fighter jet. While CarlisleIT is widely featured across commercial airframes, even in a constrained defense-spending environment, the company has been able to increase its offerings for the military market through its 2012 acquisition of Thermax and Raydex, two cable companies with deeper penetration into military aircraft retrofit programs.
“That type of thing tends to be of very good value for the Department of Defense (DOD),” said Anthony Christopher, vice president of technical operations at kSARIA Corp. “They’ve already paid for the platform, its already designed and they can make it very capable with these updates versus venturing off into a brand new platform development. And that is something that we’ve been able to benefit from here.”
An example of the demand for wire and cable upgrades internationally is the systems integration laboratory that BAE Systems plans to have constructed by the end of 2014 to support the installation of new mission computers, cockpit displays and Active Electronically Scanned Array (AESA) radars on more than 130 F-16 Block 52 fighter jets for the Korean Air Force.
Moore said TE Connectivity’s mil-spec extruded wire types and tape wrapped basic wire products qualified at AS-2275992/32 are “currently used in new military programs,” such as new production helicopters from Sikorsky’s S-76 and Black Hawk to military fighter jet F-16 and F-18 programs. TE Connectivity provides filter line wire for electromagnetic interference protection because the military environment. Helicopters, for example, are flying lower and constantly being swept by radar. “One of the issues they have is that the radar energy could have an effect on coupling and energy that would cause a flight control surface to do something the pilot does not want it to do while he’s flying,” says Moore. “So the filter line wire protects the signals that the pilot wants to get from his input to the control surface without allowing the energy from the radar sweeps to couple in.” he adds.
In Europe, Habia Cable is one of the leading suppliers of military aerospace wiring to helicopter upgrade programs. The Swedish defense manufacturer claims to have one of the industry’s thinnest single-wall constructed airframe wires with its Flight Guard product line. These wire are approved to U.K. Def Stan 61-12 Part 33 Supplement 001: Wires, Cores and Cables, Electrical Airframe Wires and Cables. Habia’s current focus is on reducing the size of its cables as the “space envelope” gets smaller and smaller, says Stefan Willmann, head of Habia’s manufacturing facility in Norderstedt, Germany. Willman believes today’s military aerospace end users desire thinner cables with thinner materials where “there is room for more cores within the same original envelope.”
Among the top aircraft wire and cable needs, more than 80 percent of Avionics Magazine readers agreed with Willmann, stating that they would like wire and cable that is smaller and lighter with higher performance standards than the airframe’s legacy wiring.
Fiber Optics
All of the major commercial and defense airframe wiring and cabling solutions manufacturers and supply chain managers agree that optical fiber cables are leading use by air framers and operators both on new production aircraft and for upgrades. Newer applications such as cockpit video technology are requiring ultra-fast data transfer rates, according to John Benzinger, marketing and products manager at PIC Wire and Cable. Results from the Avionics Magazine Wire & Cable survey show that 84 percent of operators are looking to purchase new wire and cable solutions —specifically for the installation of new avionics systems. However, the results also show that fiber optics is a growing category when it comes to data cables, as 50 percent of the respondents want high speed copper cables, and 31 percent want fiber optics.
Both in the military and commercial environment, newer avionics systems installations are requiring unprecedented usage of optical fiber. Lockheed Martin’s fifth generation F-35 fighter jet features 17 miles of copper wiring, but uses a fiber optic network for its mission systems communications. In addition to high data transfer speeds, it also provides weight reduction, says Daniel Bagby, fiber optic product manager at CarlisleIT.
“Recent fiber optic cable development at CarlisleIT has focused on improving the mechanical robustness, environmental stability, installation flexibility and general installation survivability of standard, high speed and single-mode fiber cabling and assembly products with introductions like bend-insensitive fibers, crush resistant constructions and higher temperature rated coatings and cable elements,” said Bagby. “All of these improvements make the design and integration of fiber interconnects easier on everyone from the system architect to the installers and maintenance teams.”
The ARINC Fiber Optics Subcommittee is currently in the process of updating physical standards, design guidelines and testing and maintenance procedures for fiber optic components and systems. ARINC expects to release new definitions for expanded beam contacts by the end of 2015. That will help to defeat some of the minor downsides of using current available optical fiber solutions, especially in the military environment where Duggan said “optical fiber shakes in the connector and causes leaks; … fiber still doesn’t take the bending and a lot of the vibration.”
Regardless of those issues though, decision-makers at CarlisleIT, kSARIA and TE Connectivity all agree that fiber optics is the leading solution for today’s avionics systems.
“There’s so much more fiber that is going to be on these newer aircraft and the maturity level of the knowledge base for the end users just isn’t there yet to be able to service it,” said Christopher. “Between commercial and military — both areas — all the newer platforms, the newer aircraft are putting an unprecedented amount of optical fiber into their interconnectivity.”