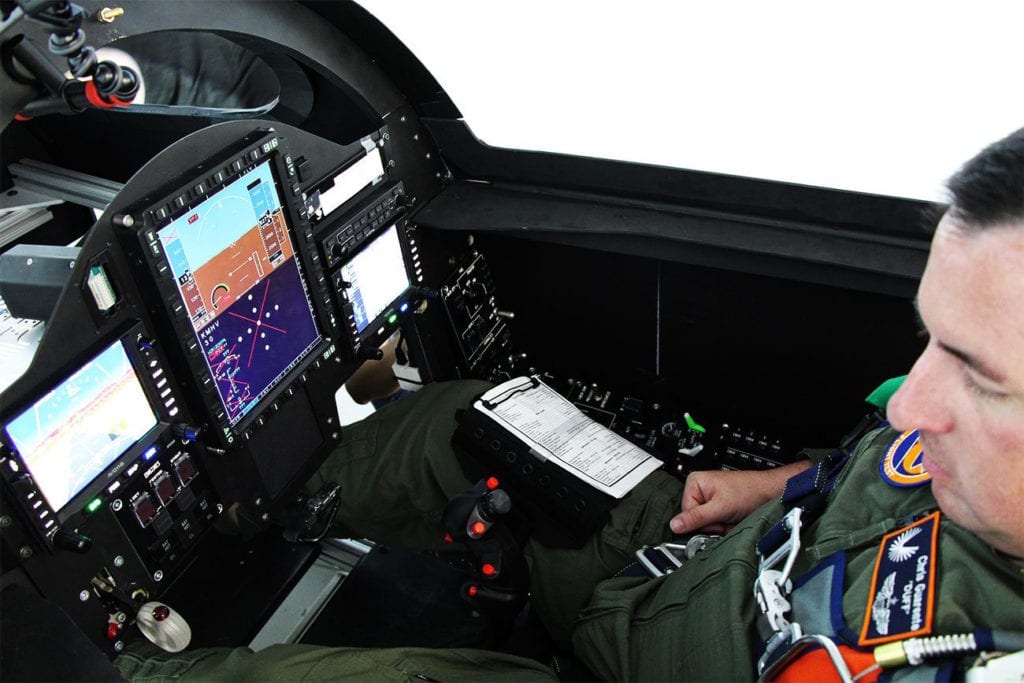
Chris “Duff” Guarente, test pilot for Boom Supersonic, sits in the XB-1 demonstrator cockpit. Photo: Boom Supersonic
As Boom Supersonic prepares for the planned rollout of its XB-1 demonstrator aircraft in December and first flight next year, Avionics International caught up with Chris “Duff” Guarente, a test pilot for the Denver, Colorado-based company, to discuss how they’re using a full flight simulator to help develop XB-1’s pilot interface.
The engineering and flight testing team at Boom has had a busy 2019, including establishing a new digital design partnership with Dassault Systèmes and another with Prometheus Fuels to supply carbon neutral fuel for XB-1. The company also closed a $100 million investment round in January, enough to advance the development of Overture, the planned production version of their supersonic passenger jet projected to enter service in the mid-2020s for launch customers Japan Airlines and Virgin Group, which have pre-ordered a combined 30 airliners.
Guarente said he and his fellow test pilot Doc have been using the internally developed simulator for more than a year and have already provided feedback to the engineering team that will lead to changes from the initial version of XB-1’s avionics components.
Avionics: What purpose has the simulator primarily served in terms of the development of a pilot interface for the XB-1 demonstrator’s supersonic flight controls?
Guarente: The purpose of the simulator is to offer a way for the pilots to evaluate the flying and handling qualities of the vehicle, provide valuable feedback to the Flight Controls Team and help make design and engineering decisions for XB-1. Doc and I have been using it for over a year, and in that time we’ve been able to review its forward-looking camera and the systems controls, as well as evaluate how the aircraft handles in-flight and for landing.
The software and hardware components in the simulator are fully flight representative. This means that the data acquisition system, the glass cockpit displays, and digital controllers are exactly flight hardware and are running flight software – there’s no special ‘simulator mode’ software running on those components. Bringing this level of realism into the simulator at such an early stage has been very beneficial for Doc and me, but is arguably even more beneficial for the engineering team. At fairly low cost and schedule risk we get to evaluate form, fit, and function of the hardware and software components long before the aircraft is available for integration. We’ve made changes to nearly all the components based on early pilot feedback, and by doing so, we can achieve multiple design iterations while the aircraft design and build is underway.

The simulator’s push-button engine start controls. Photo: Boom Supersonic
Avionics: Has your feedback led to any changes in the systems that will be featured on the XB-1 demonstrator?
Guarente: In addition, we recently upgraded our simulator to allow for significantly more capability to evaluate the control switches for each of the systems installed in the aircraft for safe operations in the supersonic part of the envelope. This allows us to develop and train on the various types of emergencies that could happen in the case of system failures. We are currently able to simulate operations and emergencies in the Environmental Control System and pressurization, the hydraulic system, the three engines, the electrical and avionics systems, flight controls, the liquid cooling system, and the fuel system.
Avionics: What are the biggest differences in terms of cockpit systems featured in the XB-1 simulator versus the type of systems that are featured in a sub-sonic simulator?
Guarente: The simulator is specific to the XB-1 aircraft and thus incorporates the many systems required for the aircraft to operate effectively once supersonic and all the way up to Mach 2.2. Many of these systems are not present in subsonic aircraft since they are not needed.
For instance, we have the controls and displays for the environmental control system that not only keeps the cockpit pressurized and cooled but will also cool other vital aircraft systems in separate bays outside of the cockpit. The outside of XB-1 could reach temperatures above 300-degrees Fahrenheit, which will cause heating throughout the aircraft; subsonic aircraft do not reach those levels so do not need to dissipate that heat.
Our simulator has all of the scheduling and controls for that system, so that we can train to use them and how to handle any potential emergencies pertaining to that system.

Some of the cockpit switches featured in the Boom simulator. Photo: Boom Supersonic
Avionics: Did Boom develop the simulator completely internally or was there any collaboration with outside companies or experts?
Guarente: The simulator is a product of Boom’s internal avionics team. This team is comprised of engineers who not only have experience on certified Level D full motion simulators but also simulators for experimental vehicles, including SpaceShipTwo and Stratolaunch.
Since initial development, our avionics, aerodynamics, and flight control teams have all played an integral role in developing the mechanical and software aspects of the simulator, which has allowed us to incorporate our aircraft flight model into the simulator. We’ve also been able to include our data acquisition system, which lets us test the aircraft throughout its entire flight envelope, along with the flight control systems that help us fly the aircraft in the loop.
Avionics: How will the use of this simulator inform Boom on the development of the real cockpit for its first supersonic commercial production airplane design?
Guarente: The simulator has already helped us identify pilot-to-vehicle interface (PVI) modifications that we will implement and test further in the simulator and then on the XB-1 demonstrator. Further simulator evaluations as the design and build of XB-1 progress will allow us to directly measure increases or decreases in pilot performance with modifications to the displays and controls.
For instance, XB-1 has a forward looking camera system (FLVS) to aid the pilot in landing the aircraft. This system is being integrated by our avionics team and its display is currently being tested in the simulator. It will ultimately be used to assess each display modification for pilot performance improvement or degradation for landing, allowing us to iterate many display designs to perfect them prior to flight. These lessons and display techniques will then be used in the follow-on Overture aircraft to ensure the highest level of safety and pilot proficiency across the supersonic fleet.
Correction: The article has been updated to note that Boom’s simulator is not Level D, and the $100 million round of funding was to advance the development of Overture.