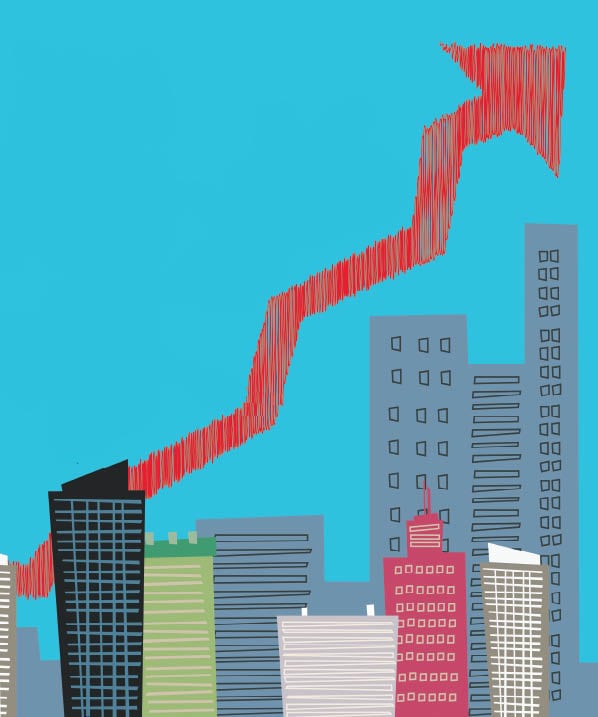 |
|
If you’re involved in the aviation technology industry in any way, chances are you’ve been inundated with reports, headlines and news coverage of the commercialization of Unmanned Aircraft Systems (UAS), also known by the European Aviation Safety Agency (EASA) term, Remotely Piloted Aircraft Systems (RPAS). With such buzz, we were surprised to receive a relatively low number of responses to our Upgrade Central survey dedicated to Unmanned Aircraft Systems (UAS). This is especially surprising considering some of the biggest names in the mainstream avionics industry are currently involved in ongoing research around commercial UAS. Honeywell, for example, is involved in an ongoing research project with NASA and General Atomics Aeronautical Systems Inc. (GA-ASI) flight testing autonomous sense-and-avoid technology. Rockwell Collins’ October 2014 flight demonstration in partnership with the University of Iowa College of Engineering, which showcased the ability of its flagship Pro Line Fusion flight deck to be used as a surrogate ground control station, is another good example. What we did learn from the survey though, is that 71 percent of Avionics readers are operating UAS commercially and 46 percent have needs to acquire new avionics equipment or components for their existing aircraft.
It is possible the lack of responses reflects that, even in 2015, the industry is still in the early stages of growth. Despite the FAA issuing 500 commercial exemptions for what it refers to as commercial UAS operations, all of those involve the use of small-sized unmanned aircraft being controlled for low-level operations within line of sight below 500 feet — something hobbyists have been doing for years. We interviewed some of the leading manufacturers and technology developers in the industry today to find out what technologies they’re testing right now, which onboard avionics are available now or in the works to enable the types of large-scale bellow-line-of-sight (BLOS) operations that truly define what we can expect in the not-so-distant future for commercial UAS applications.
OEM Perspective
 |
Predator B Due Regard Radar. Photo: GA-ASI. |
Boeing subsidiary Insitu and GA-ASI supply and operate commercial-ready UAS in the sense of the traditional focus of our Upgrade Central articles: providing airframes that can be purchased and re-configured with new technology to improve performance and operational efficiency while also lowering the cost of maintenance.
General Atomics’ Director of Strategic Development Robert S. Dann, says the company sees the commercial UAS market as a major growth industry, well beyond what the manufacturer’s Predator line of drones have traditionally been used for in the military environment.
“The small UAS industry is important because it is really a mode of transportation, and shows what the early commercial environment in this industry could look like. Though the smalls are characterized as what people call drones, it is quite different than the aircraft we build, which are more in the traditional sense of a manned aircraft in terms of capability that and the ability to participate in the regular manned National Airspace System [NAS]. The larger the aircraft, like ours, it’s able to be equipped with the proper equipment to participate in the NAS,” said Dann. Currently, GA-ASI, NASA and Honeywell are flight testing a Predator B UAS known as the “Ikhana,” which features a reconfigured avionics package that includes manned aircraft technology that civil aviation regulators aren’t quite yet ready to certify on Unmanned Aerial Vehicles (UAVs). The type of testing that it’s currently undergoing should help with that, however. The modified Predator B drone has a 66-foot wing span with an internal payload capacity of 850 lbs., featuring a Military Standard (MIL-STD)-1760 stores management system, C-band line of sight data link control, and Ku-band satellite communications data link for BLOS control.
“Navigation systems, a [Traffic Collision Avoidance System] TCAS box, transponders — those are all avionics that we have already integrated into our aircraft. However, the FAA is not ready yet for TCAS and that more traditional [Federal Aviation Regulations] FAR 91 type of equipment to be adopted yet for UAVs. But we have them in there in a passive mode so we can understand what aircraft is around us and how the technology works on a remotely piloted aircraft,” said Dann.
Insitu’s flagship UAS, the ScanEagle is much smaller than the Predator, but it is one of the most robust UAS platforms on the market today, which has already proven its worth in commercial and civil operations, such as the June 2015 BLOS flights conducted in Denmark. The ScanEagle was launched from Hans Christian Andersen Airport (HCA) and flew within a predefined airspace corridor over the Odense Airport, Odense Fjord and Kattegat before returning to its original destination. “From an avionics perspective the improvements over the years have been transitioning away from analog sensors and feeds to digital feeds, digital video or the use of digital data networks onboard the aircraft. The other major progression has been progressively increasing the amount of electrical power, which drives the customer’s ability to use more complex and more numerous payloads on a given aircraft,” said Insitu Vice President and Executive Chief Engineer Pete Kunz. “On the core system, we tend to take an approach of a stable core avionics architecture with flexibility on the peripherals. By peripherals that may be payloads, radios and communications even extending to the propulsion.”
Much like GA-ASI, Insitu is also introducing technology traditionally reserved for manned aircraft onto the ScanEagle to improve its ability to report its position within the NAS and safely fly around other aircraft.
“Going forward we’ll be very shortly introducing Automatic Dependent Surveillance – Broadcast (ADS-B) into our platforms,” said Kunz. “With ADS-B, whether its through a simple supplier relationship, we will consider third party vendors or, in some cases, partnership or co-development. We will definitely leverage outside sources who are better than us at developing those pieces of technology. What we will bring to the table with ADS-B is a determination of how those technologies are integrated into our aircraft and our core existing avionics architecture, because that has not really been done yet from an unmanned aircraft perspective.”
Sense and Avoid
Sense-and-avoid is more than a buzz term for developers and manufacturers in today’s commercial UAS industry, it is a technological barrier that chief technology officers, engineers, and manufacturers are looking to move past. Right now, Radio Technical Commission for Aeronautics (RTCA) Special Committee 228 is developing the Minimum Operational Performance Standards (MOPS) for sense and avoid, and expects to have the final standards complete by July 2016. But there are technologies available today on a smaller scale that do provide sense-and-avoid capabilities.
 |
NASA’s Ikhana Predator B Drone is being used in sense and avoid flight testing. Photo: GA-ASI. |
“The sense-and-avoid system that we’re currently testing consists of our Due Regard radar, plus it is tied in with TCAS and will eventually be tied in with Airborne Collision Avoidance System (ACAS), as that’s going to be the replacement for TCAS and it will accept inputs from all three of those components. That’s what is called the sense-and-avoid system,” said Dann. “This is a system that will basically generate a predictive bubble in the ground-based pilot’s display much like a cloud. It shows him a cloud, with vertical and horizontal dimensions predicting zones where, if they keep flying, they will end up colliding with another aircraft. So, basically, you have to avoid those yellow clouds. They’re predictive zones and, as you can imagine, the closer you get to an object, the larger that cloud is going to grow because it indicates a reduced possibility that the operator has to maneuver around that aircraft. If you don’t manually maneuver the aircraft around the oncoming object, it will execute an automatic maneuver to avoid that object.”
Those who are part of the masses applying for FAA commercial UAS exemptions or looking to operate smaller scale UAS in other parts of the world for infrastructure inspections, surveillance, or to get up close pictures inside of a petrochemical tank, will want to have a discussion with Panoptes UAV Chief Technology Officer Fabrice Kunzi, or Panoptes Vice President of Product Development Elena Micich. Panoptes, a spinoff of Aurora Flight Sciences, has developed the eBumper4, which is an obstacle avoidance retrofit kit that currently supports the DJI Phantom 2 and the 3DR Iris+ small UAS — two of the most widely used UAS in operations that have been approved by the FAA through a Section 337 exemption. When the eBumper4 senses an obstacle in its field of view, it activates to reduce the likelihood of a collision, and then “bumps” the aircraft away from the obstacle before returning control to the operator.
“A common theme that we’ve seen by having a technology like the eBumper is that it is really a low-cost, low-power obstacle avoidance add-on. People in the enterprise and commercial space are in the idea stage; they’re saying ‘hey, I have some ideas of how I’m going to use drones but I’m nervous about flying drones around my infrastructure or inside a petrochemical tank or near my cell tower,’” said Micich. “With obstacle avoidance they can do that more safely. The demand we’re seeing is people saying ‘hey, I want to test out drones but I want to do it safely.’ That gives us a lot of information about how people are actually thinking about the use of drones. Inspecting power lines, inspecting roofs, or placing a drone inside a large petrochemical tank so there’s no need to build a scaffolding and have a guy actually walk in there and take pictures. Cell tower inspection — it is literally all over the place.”
Even aerospace and defense industry power players, such as Curtiss Wright, are getting into the growing commercial UAS avionics race. In May, the manufacturer’s Gigabit Ethernet (GbE) switch subsystem technology was used in a High Altitude Long Endurance UAS, the kind that is designed with solar-powered cells and has the ability to fly for several days and even months — in some instances — at a time. This is a trend where Curtiss Wright sees growing demand within UAS platforms; the ability to provide sophisticated processing power and meet MIL-STD specifications in smaller form factors.
“One of the biggest things we’re seeing — and this is not just with UAVs, but really sort of the Internet of Things world — is the ability to do more and more processing out on the edge. We tend to view the UAV itself as the edge device, a platform for a lot of different sensors performing collection of data, onboard analysis, algorithms and boiling the results of that number down to present information in a meaningful way to the end user of that platform,” said Curtiss Wright Chief Technology Officer David Jedynak. “The biggest thing we’re doing is with smaller and smaller form factors. There’s a standard board and backplane type VPX standard that we design around, and we’re also providing ultra small form factor type switches and processors that are well-suited for the smaller UAV market. One of the ultra small form factor networking boxes are literally pocket sized. That’s the beginning of a broader product family for us that will include storage and video processing and small mission computers.”
Ultimately, achieving true widespread usage of UAS for complex commercial missions will require an industry-regulatory culture change, where a lot of interdependent elements have to come together.
“This evolving industry involves onboard aircraft technology, infrastructure changes or verification, policy and regulation, as well as implementation first with testing and then slowly deploying it nationwide and then worldwide — and we’re not the only ones looking at it as a race. The International Civil Aviation Organization [ICAO] is working on global standards. The Europeans are working on airspace, everybody sees it as a means to get ahead of everybody else and create jobs for their country,” said Dann. “We are at the tipping point right now. Sense-and-avoid seemed to be the one piece that was stopping everything. People can think beyond that now and the vision and list of things that need to be done have been developed. It is a field that is going to start growing fairly quickly.”
Three UAS Industry Projects Worth Watching
1. Pathfinder Program: In May, the FAA approved the Pathfinder Program, the first within domestic U.S. airspace approved by the Civil Aviation Authority (CAA) to test BLOS commercial UAS operations. Under the program, UAS manufacturer PrecisionHawk will use its Lancaster fixed-wing small UAS to fly BLOS operations to collect data on crops for farmers as well as to fly hundreds of miles to inspect railroads operated by BNSF Railroad. Panoptes UAV Chief Technology Officer Fabrice Kunzi says that these types of unique operational environments are exactly what the company designed its Panoptes Core technology for, which is a hardware and software solution that uses different sensors on the aircraft to detect different operational threats.
“The vision that we have for the introduction of these unmanned aircraft into our daily lives is that we need to protect across a very large range of different potential threats or collision possibilities,” said Kunzi.
2. Facebook: On July 1, Facebook co-founder and CEO Mark Zuckerberg unveiled the latest developments about the social media giant’s ongoing commercial UAS research project. The aim is to provide connectivity to grant 3 million people access to the Internet in rural areas of Africa and Asia where there is no existing infrastructure. Facebook’s connectivity lab is developing a laser communications system capable of beaming data from the sky into communities, which Zuckerberg notes can dramatically increase the speed over long distances.
The technology entrepreneur has previously revealed that the final design of the high altitude solar powered UAS that it is developing in collaboration with Zephyr and Ascenta will have a wing span greater than a Boeing 737 and will be capable of flying at 65,000 feet for several months.
3. DHL: DHL Parcel has been conducting BLOS trial flights in Germany of its own “Parcelcopter,” performing aerial delivery of medical supplies to the island of Juist in the North Sea. The Parcelcopter’s maiden voyage occurred in December 2013, and the postal company has been using it to fly along a 12 km flight path to the island as an alternative to traditional ferry transport of supplies. While the flights are completely autonomous, they’re being constantly monitored by a ground station in Germany that serves as a liaison with German Air Traffic Control (ATC).
To ensure safety and security, this type of BLOS operation should look to incorporate DO-178C design assurance into the airborne systems software used to control the aircraft, according to AdaCore Senior Avionics Engineer Dudrey Smith. DO-178C is the primary standard used by the FAA and EASA to approve commercial software-based aerospace systems.