The engineering required to design, build, operate and maintain modern aircraft is no less than a monumental feat. Hardware, software and integration challenges have been solved by many hours of effort from countless engineers. For example, modular racking circuit card assemblies now comprise the majority of the hardware architecture, moving away from traditional line replaceable electronic or mechanical units. And compared to just 20 years ago, the level of integration between systems is immense and inseparable.
Now imagine building a replica of an aircraft with additional systems, hardware, software, inputs and outputs. These also require seamless integration into your replication. Also, you must add much more specialized functionality. And as an engineer, you realize that much of this additional work could have, and should have, been designed into the architecture in the first place. Congratulations, you have just built a flight simulator.
Flight Simulation Training Devices (FSTD) are complex systems that require unique capabilities to provide efficient training to aircrews. These capabilities allow the FSTD to be rapidly configured to maximize the available training time. These capabilities and functionalities are defined by ARINC Report 610: Guidance for Design of Aircraft Equipment and Software for Use in Training Devices, which outlines the specific needs of the flight simulation industry, including guidance for implementation, description of functions, documentation requirements and case examples of proper and poor implementation in civil aviation FSTDs.
The Flight Simulator Engineering and Maintenance Conference (FSEMC) delegates consistently rank the lack of ARINC 610 functionality in their top five engineering challenges. In response, the FSEMC chartered a working group to create ARINC Report 610 (currently at Revision C). The working group consisted of subject matter experts from airframe manufacturers, training device manufacturers, avionics suppliers and airlines.
Because of increasing air travel, fuel costs, as well as the continuing need for trained pilots, the flight simulation training industry is a vital part of the aviation industry. Flight training is expensive, and using a flying aircraft in a non-revenue training scenario is, in most cases, simply not an option.
FSTDs are a less-expensive option than operating aircraft and are the next best thing for aircrew to either learn new flight procedures or practice emergency and abnormal procedures. Simulators are often in use training aircrews 20 hours out of a 24-hour day. In a four-hour training session, every minute counts.
Consider when a crew first gets into a Full Flight Simulator (FFS) for a training session. Before they take off, they must enter a flight plan in the Flight Management System (FMS). Often, this can be a quite lengthy procedure. During this time, the aircrew is heads down, using the keyboards and not using any other parts of this very expensive FFS. The rest of the simulator is idle. This uses 20-30 minutes of expensive simulator time.
There is a solution to this, and it involves the avionics found on the vast majority of airframes flying today. Aircraft equipment and software developers provide functionality in their products specifically for flight simulators. Although not all inclusive, a short list of these capabilities includes flight freeze; reposition; weight change; wind change; fuel freeze; snapshot upload; and snapshot download.
ARINC Report 610 uses analogies to explain the defined functions. For example, a Fuel Freeze for an automobile would result in the car being able to travel any distance without affecting the level of fuel in the tank (nice feature if you can find it). Similarly, an analogy of Snapshot Upload is already a reality in some automobiles. By recognizing a unique key device, the car will move the seat, the steering wheel, and set the environmental system to the saved settings by that user of the key.
Moving from cars to planes, let’s return to our example above. The training instructor could use the Snapshot Upload/Snapshot Download functions to record the flight plans that are being used in this (and other) training sessions ahead of time. When it is time to enter the flight plan, it is simply copied into the simulator’s Flight Management Computer (FMC) using the ARINC 610 function. You have just saved 12 to 15 percent of very expensive simulator time (time equals money, especially in the aviation industry). That saved time can then be used for other valuable training maneuvers that make more use of the full FFS capability.
Another time saving example involves the use of the Reposition and/or Flight Freeze functions. An aircrew training on missed approaches benefit greatly by being able to quickly slew the aircraft position to 10 miles on final, flying the approach, and having the instructor freeze the simulation to immediately provide feedback to the aircrew.
Without these features, the aircrew must fly time-wasting circles around the subject airfield and then wait to receive feedback in the classroom debrief.
In addition to the aircrew time and workload, instructor workload is a concern. Without simulator-specific features, the instructor may spend an exorbitant amount of time managing the device and not the training session.
The design of avionics equipment and software is a long and arduous process. The added time for integration and certification of adding ARINC 610 functions is sometimes sacrificed at the altar of saving time/money. However, a direct effect of excluding ARINC 610 functions is the cost of developing workaround solutions for multiple simulators, and continuing the maintenance of flight simulators using workarounds. Keep in mind that these flight training devices, similar to flying airframes, are used for 25+ years.
From a training device manufacturer’s point of view, integrating existing aircraft equipment with ARINC 610 functions results in less expensive development costs, which in turn allow airlines and operators to acquire simulators at a lower initial cost. After purchase, the maintenance of the devices is also lower because there are fewer engineering changes to provide simulator-specific capabilities. As any engineer knows, it is easier and cheaper to design for success than to design to correct failures.
Similarly, from an airline’s point of view, airplane purchasing decisions necessarily include consideration of training of the aircrew on the new type. While acquisition cost of the airframe and avionics equipment could be initially lower if the unseen ARINC 610 capabilities are not incorporated, the cost of flight simulation device acquisitions would be higher for all of the airlines establishing simulator capabilities. The airlines will then also incur the cost of additional engineering and maintenance over the lifetime of the training device.
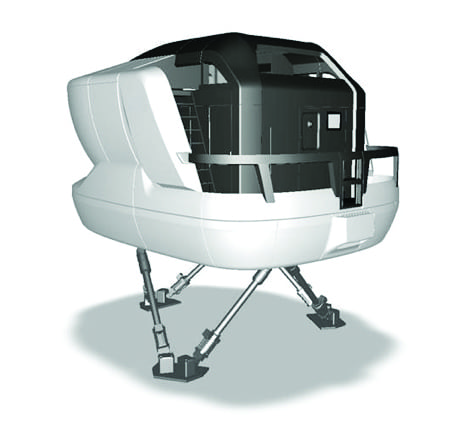 |
Full flight simulator |
There are regulatory requirements that apply to simulators as well. ICAO 9625, Manual of Criteria for the Qualification of Flight Simulators, requires the FSTD be assessed to ensure that repositions, resets and freezes support efficient and effective training. Similarly, FAA regulations require that the simulator should be capable of operating reliably after the use of training device functions such as repositions or malfunctions.
Consider the maintenance efforts to keep the device at the required fidelity, as well as supporting the training capabilities required by regulatory authorities, over a 25-year timeframe. System upgrades generally require new software, or even hardware interfaces, to be integrated into the device. This invariably results in a considerable amount of time for testing the systems and testing the device as a whole. Including the time required to re-qualify the simulator, the device could be unavailable for aircrew training for a significant amount of time while upgrades are installed and tested. If all of that isn’t enough, when another upgrade is required, the work to enable simulator-specific functions will begin again. More training availability time will be lost.
A majority of this work could be avoided if the newly acquired airframe avionics systems incorporated ARINC 610 functionality. The training device manufacturer could build and integrate more efficient devices, and the airline would see better efficiency in the use of the device in training. Over the 25+-year life of the training device, less engineering and maintenance resources will potentially return savings (and possibly revenue if training time is sold to outside organizations) to the airline.
Scott Smith is a staff principal engineer at ARINC Industry Activities, and is the assistant secretary for the FSEMC. He can be reached at 410-266-2805, or at [email protected]. The next FSEMC conference will take place Sept. 15-18, 2014, in Tulsa, Okla. For more information, visit www.aviation-ia.com.