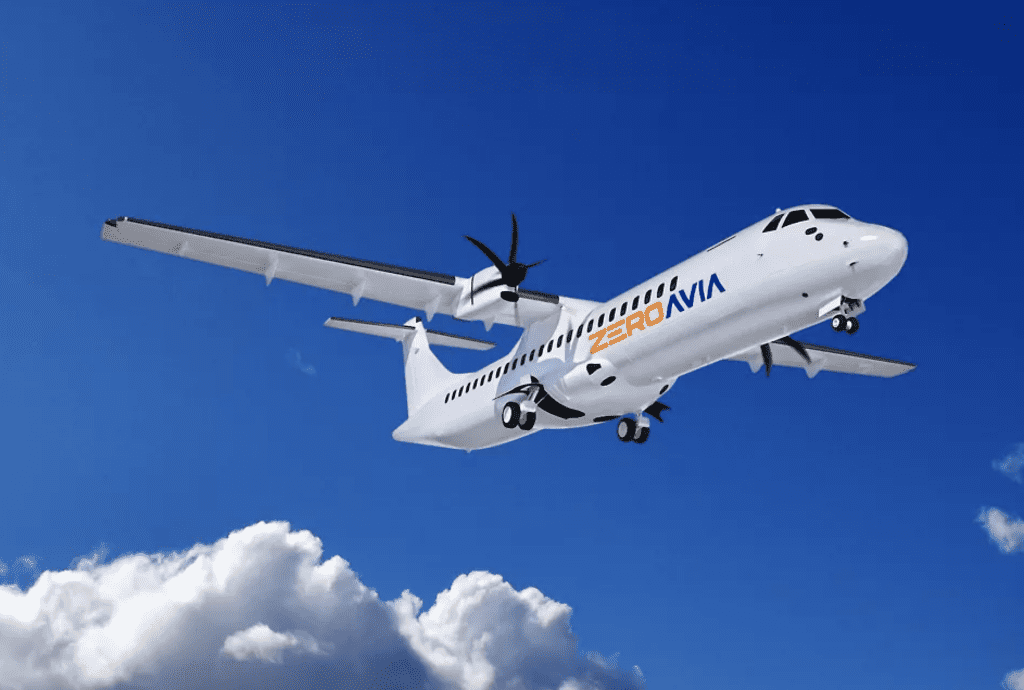
Ansys and ZeroAvia are working together to develop a hydrogen-electric powertrain using simulation technology. (Photo: ZeroAvia)
Ansys, a leader in engineering simulation, entered into a partnership with ZeroAvia for continued development of ZeroAvia’s new hydrogen-electric powertrain. Ansys enables companies to create digital models of their product during the design and development phases. Many of the company’s key customers are involved in aerospace and defense, and Ansys also enables simulations for other industries such as automotive and energy.
Ansys has been working with L3Harris Technologies and the U.S. Army Combat Capabilities Development Command since 2020 to advance the use of the FACE (Future Airborne Capabilities Environment) technical standard for cockpit displays. Ansys provides its SCADE software toolset, which is designed to enable a complete workflow.
Avionics International recently caught up with Walt Hearn, Vice President of Worldwide Sales & Customer Excellence at Ansys, to learn more about ongoing efforts at the company as well as the partnership with ZeroAvia. Check out our question-and-answer session with Hearn below.
Avionics: What advantages does Ansys offer its customers?
Walt Hearn: Using our technology, companies are able to test all of the different variations so when they build a physical prototype, it works as intended. For example, in the aerospace and defense industry, we do all of the external aerodynamics to understand airflows, lift, drag, et cetera, in a digital model before building.
We do all of the lighting and the avionics inside the airplane—how do the antennas connect to the ground, headset displays, embedded control software. We simulate everything from a semiconductor inside the cockpit and the display to the full airplane and the full mission of an airplane or a satellite. Everything we do is purely about simulating the physics. All of the major aerospace companies use our technology to design their products.
For the aerospace and defense industry in particular, what are the biggest challenges or hurdles that you’re facing?
Hearn: The biggest challenge or opportunity we see is a huge transformation going on inside the aerospace industry. It’s the complete redesign of airplanes, of eVTOLs that are coming to market, fully electric airplanes—that’s a huge engineering challenge. You have a lot of new and existing companies coming into the market designing eVTOLs.
It’s also a huge opportunity because of the redesign of all these new platforms. We haven’t seen this much change in the aerospace and defense industry in the last 50 years, which is tremendously exciting for us and the industry.
It’s impossible to physically build all of the new systems that are being designed—electric drive systems, hydrogen-electric—and physically test them.
We have this huge transformational shift coming about in the aerospace industry, and the engineers have to test all of these variations. They’re doing that in simulations. They’re having to design new lithium batteries and connect the new batteries to the system because the range of batteries on the market today isn’t long enough for what we’re looking for.
Could you tell us more about the partnership with ZeroAvia?
Hearn: We’ve been working with ZeroAvia for a while. They’re developing a new propulsion technology. It’s exciting to see startup companies like ZeroAvia coming after this big challenge with a new propulsion system that enables them to get closer to zero emissions.
For this new propulsion system, we have to simulate all of the different applications in the powertrain: simulate how the new motors work, and how the fuel tanks compress hydrogen fuel safely. They’re using our tools to simulate the structure and mechanics of these components. ZeroAvia is testing hundreds of millions of variations and optimizations in a virtual environment so that the platform will perform as seen. It drives down the cost of building physical prototypes.
It’s a new company so they’re able to leverage these new digital technologies that are in the market today to create a propulsion system that is not only going to be great technology but going to be great for the environment.
Can you share details of any other ongoing efforts or projects at Ansys?
Hearn: We’re working with the University of Central Florida and NASA on a $10 million five-year project. We’re working on different sustainable fuels for aircraft, such as hydrogen. UCF, NASA, and Ansys are working on next-generation fuels and research of fuels that can be used in different propulsion systems for different aerospace and defense applications.
We also enable companies to look at the life cycle of the material they’re using inside their product. We have a tool called Granta, a materials management software that enables engineers to look at the life cycle impact of different materials on the design they’re using They choose the optimal material based on its CO2 footprint and also on its viability inside the design.