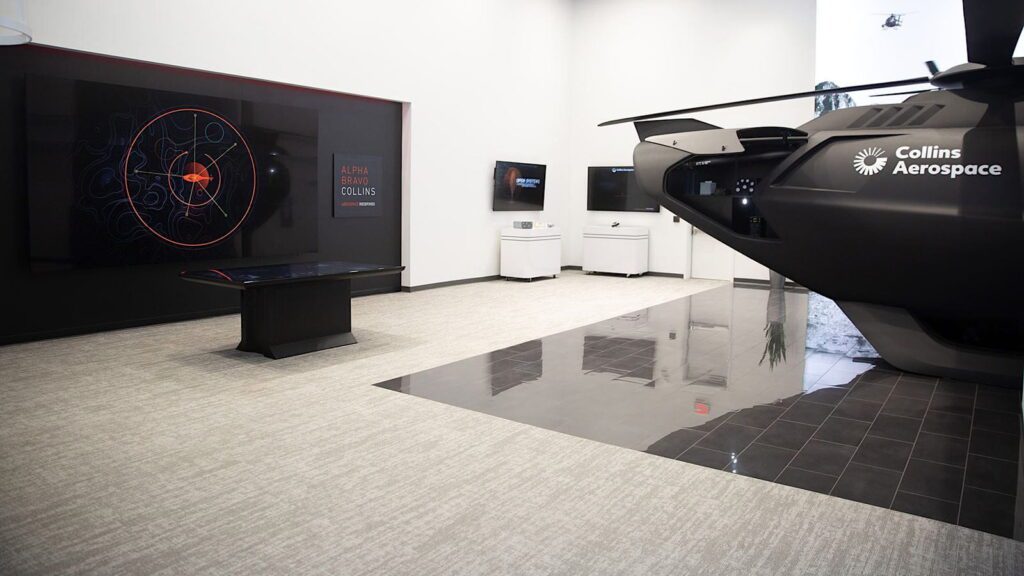
The Collins Aerospace Customer Experience Center in Huntsville, Alabama (Photo: Collins Aerospace)
HUNTSVILLE, Alabama — The U.S. Army has signed a Cooperative Research and Development Agreement (CRADA) with Collins Aerospace to develop a new approach to airworthiness certification of multicore processors and safety critical systems modularity. During a Sept. 28 media briefing held at their Customer Experience Center in Huntsville, engineering leadership for Collins Aerospace explained how their work with Army aviators will advance the adoption of Modular Open Systems Architecture (MOSA) across the various manned and unmanned aircraft they operate.
CRADAs are used by the Army and other federal agencies to allow for the exchange of government equipment, facilities, and resources with non-federal entities. During the CEC media briefing, Collins showed prototypes of how the use of MOSA embedded computing form factors can reduce the number of individual computers required to enable communication, navigation, and surveillance applications on the Army’s enduring and future fleet of aircraft.
Computing performance expansion enabled by multicore processors is the result of linking multiple central processing unit (CPU) cores that share the tasks necessary to run an application into a single unit. This allows for the sharing of tasks and resources such as cache memory that would usually be separated out among multiple computers, to be run using the multiple cores of the singular processing unit.
Embedded systems suppliers and avionics manufacturers have been working toward achieving such a safety-critical milestone for many years, as the majority of in-service avionics systems rely on single-core processors. The interference that can occur when multiple processing cores are used to develop a computer system has been a certification challenge in the past, although Collins and other companies have advanced multicore processor-enabled avionics in recent years.
Based on this use of multiple processing cores within the same processor device, most of the communications, navigation, and surveillance applications of an aircraft that used to require an individual computer for each LRU can be enabled from MCPs working from assigned processor slots in a single chassis.
Tom von Eschenbach, program manager for Army Avionics at Collins, said that the certification of modularity and multicore processors remains one of the most challenging areas of the Department of Defense’s aircraft and technologies procurement process. A major goal for the work Collins will perform under the CRADA is to help the Army adopt new technologies faster throughout the life cycle of in-service aircraft.
“Why is MOSA so important? Why is MOSA one of General Rugen’s four lines of effort within the FVL cross-functional? It depends on who you are and what you value, and sometimes your answer is a little different,” von Eschenbach said. “The goal is not to procure an aircraft that had technologies designed in the early 2020s, produced in the 2030s and then to be operated with those same technologies for 20 years. You have to figure out how to introduce new technologies in a continuous process.”
Collins engineers at the CEC are already coming up with prototype designs that aviation program leadership from the Army can evaluate with hands-on simulator and flight testing.
One such MOSA-inspired prototype at the CEC is FlexLink, a technology that Collins describes as an adaptive-connectivity system for aircraft where communication, navigation, and surveillance (CNS) capabilities can be inserted, removed, upgraded, and re-inserted or replaced as processor cards. FlexLink’s form factor and purpose served as the central processing box on the aircraft is an example of the type of embedded avionics computing configuration that the Army’s MOSA Transformation Office describes as its vision for future open systems architecture.

Mosarc is the MOSA avionics architecture Collins has developed aligned to the open systems architecture the Army seeks to embrace. (Photo: Woodrow Bellamy III)
“We’re flying a FlexLink prototype at this year at Project Convergence,” Chadwick Ford, associate director of the Army JADC2 requirements and demonstrations team for Collins Aerospace, said during the media briefing.
The architecture and purpose served by FlexLink is also aligned to the Army’s CMOSS Mounted Form Factor (CMFF), a standard “plug-and-play” approach explained in a July 2021 post by the Army Program Executive Office (PEO). CMFF uses the C5ISR/EW Modular Open Suite of Standards (CMOSS) confirmation that gives the Army the ability to “insert cards, each embedded with networked capabilities such as Positioning, Navigation and Timing (PNT), mission command applications, or radio waveforms, into a common ruggedized chassis” inside a tactical aircraft or vehicle, according to Army PEO.

This prototype chassis developed by Collins shows the type of card-based architecture that the Army wants to adopt for current and future aircraft systems. (Photo: Woodrow Bellamy III)
FlexLink also provides the type of form factor and functionality envisioned by the Army’s Aviation Mission Common Server (AMCS) initiative first launched for its helicopter fleet in 2020. A MOSA panel discussion presentation held during the 2022 Army Aviation Association of America (AAAA) provides several references to concepts other companies are developing that also focus on providing all of the processing necessary for an aircraft’s individual avionics applications from a single chassis.
Mercury Systems also has a video overview from its AAAA exhibit demonstrating how the AMCS-architected system they have developed consolidates processing managed by multiple boxes on typical in-service Army aircraft into a single chassis.
Collins has also previously demonstrated MOSA avionics concepts in partnership with Army, including a multi-domain operation (MDO) demonstration during the September 2021 Future Airborne Capability Environment (FACE) Technical Interchange Meeting (TIM). The demonstration, lead by Collins Aerospace, featured software and multiple third-party mission computers—including Parry Labs’ Stellar Relay—integrated into a helicopter flight deck.

The helicopter simulator cockpit at the CEC (Photo: Woodrow Bellamy III)
Harold Tiedman, technical fellow and Collins’ chief engineer for FVL, said the CRADA signed with the Army is also aimed at changing how military aircraft and their mission-specific technologies are acquired, operated, and upgraded.
“With the CRADA and the integration of more systems into these smaller form factors, we’re also really challenging the norms of how procurement is done,” Tiedman said. “Traditionally, the customer or the OEM would buy a computer, you’d buy an environmental control system, a generator, and a health monitoring system, as an example. Those things are all separate systems. But what they all have in common are central processing and control elements. If we can eliminate those individual control elements and integrate them together, now you’re able to reduce the number of boxes and the amount of wire in the aircraft required for each.”