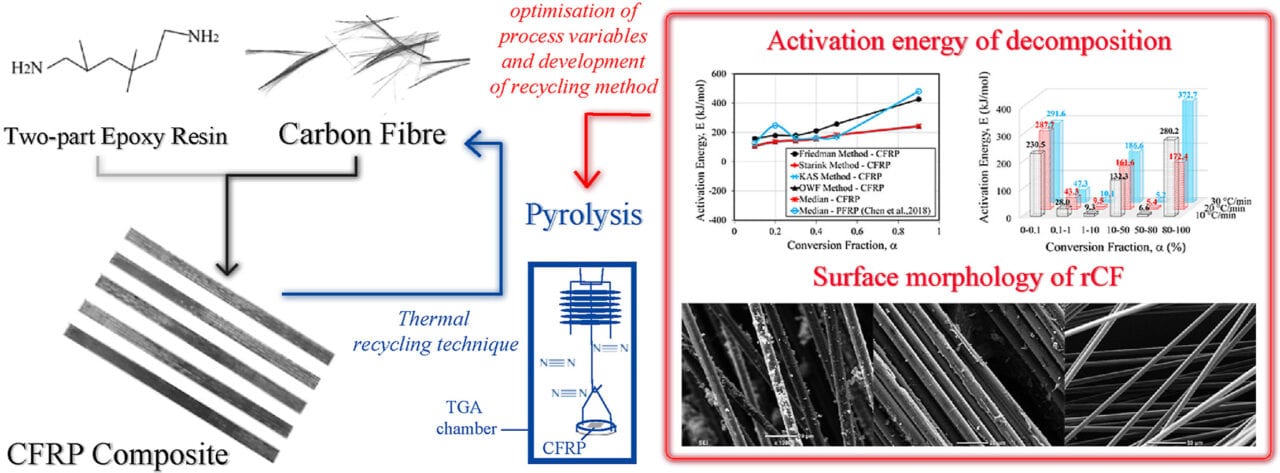
A team of engineering researchers from the University of Sydney have developed a new method of combining pyrolosis and high temperature oxidation to recycle and remanufacture carbon fiber composites without materially weakening its properties. (The University of Sydney)
Researchers at the University of Sydney have developed an improved process for recycling carbon fiber reinforced polymer (CFRP) composites that are featured in modern commercial airframes.
A new study published by the Australian school outlines their method of recycling CFRP composites while maintaining up to 90 percent of their original strength, making them more viable for re-use in the airplane manufacturing process. Dr. Ali Hadigheh, who leads the University of Sydney’s research team, told Aviation Today that the recycled composites, when their original strength is maintained, are suitable for airframe sections with “strong curvature or sharp edges.”
“In this research, we are focusing on both recycling, and remanufacturing of composites from recycled carbon fiber. The main challenge with recycled carbon fiber (rCF) is that rCF is short, fluffy and discontinuous. Currently, rCF is mainly used in nonwoven forms using automated composite manufacturing techniques (ACMTs),” Hadigheh said. “Nonwoven composites made of filamentous and random fibers can achieve fiber volume fraction (FVF) of maximum 30-40 percent. Methods such as carding, combing and grilling have been successfully used to improve orientation of fibers, however, these intense mechanical processes are likely to cause severe damages to the rCF. We have been working on this aspect as well and currently have a patent for realignment of fibers. This enables us to precisely control the fiber orientation and also push FVF of recycled composites to higher values which would be suitable for the use in airplanes.”
Hadigheh’s research describes CFRP composites as anisotropic materials with high strength-to-weight ratio and corrosion and wear resistance that makes them ideal for use in aircraft parts, wind turbines, automobiles and consumer products like laptops and smartphones. As manufacturers across multiple verticals have increased the use of CFRP in new products, they have also increased associated waste, which is harder to recycle with CFRP because of the way it is developed.
The type of CFRP composites used in the newest airframes is developed with a glue-like polymer that bonds carbon atoms together into individual carbon fibers, which can then be used in woven and non-woven configurations to support a manufacturer’s desired structure or shape.
“Globally and in Australia, there has been a march towards better recycling processes, however, there is often the belief that a material can be recycled an infinite amount of times – this simply isn’t the case. Most recycling processes diminish mechanical or physical properties of materials,” Hadigheh said.

CFRP samples for thermo-gravimetric analysis (TGA) were carefully cut with scissors into small pieces with weight range of 10 ± 2 mg. Careful attention paid to ensure all specimens had similar fibre to resin ratio, according to the study.
Until now, however, the global manufacturing supply chain has found it challenging to recycle and reuse carbon fibers, especially in new airplane parts, because most of the existing recycling methods involve shredding, cutting or grinding the fibers in a way that wears the material down making it too weak materially to reuse in a new product.
Hadigheh believes the advancement of their new process could help enable a more “circular economy” for aerospace manufacturers, and other manufacturing supply chains, where resources are redeployed and reused and waste flows are turned into inputs for further production.
Their method involves pyrolysis to break the carbon fiber material down using heat and oxidation, which uses higher temperatures to remove the chars imposed on the materials by the pyrolysis process.
“The pyrolysis process consisted of two stages: in the first stage, CFRP coupons were heated up to 425 degrees Celsius in intervals of 20 C/min. At the end of this stage approximately 55 percent of the matrix is removed. To avoid fiber oxidation during the pyrolysis, an inert atmosphere was created by nitrogen with a gas flow rate of 60 mL/min. After pyrolysis stage, oxidation of the CFRP up to 550 degrees Celsius at a dwell time of 45 minutes as the secondary recycling method was employed. During these tests, a TA Instruments Q50 thermo-gravimetric analyzer (TGA) was used to monitor the mass change due to thermal decomposition of specimens,” Hadigheh said.
By investigating the physical characteristics of the recycled fibers using a scanning electron C, the research team further observed that pyrolysis of the composite material remains efficient until 425 degrees Celsius. A second oxidation stage of up to 550 C is required to achieve the production of recycled carbon fiber products that maintain at least 90 percent of the original material’s efficiency and strength.
Aerospace OEMs have been investing in initiatives to improve the recycling process for carbon for a number of years. Boeing for example earned a 2020 Sustainability Leadership Award from the National Association of Manufacturers (NAMA) in recognition of their efforts to reduce waste produced by their use of carbon fiber composites in their aircraft such as the 787, which features 23 tons of the material.

A July 2020 Boeing article gave an update on their carbon fiber recycling partnership with UK-based ELG Carbon Fibre Ltd. (Boeing)
Boeing has been partnering with U.K.-based ELG to collect scrap metal from carbon fiber composites produced by 11 of their manufacturing sites across the U.S., Europe and Asia and recycle the excess material using a furnace to vaporize the resin that holds the carbon fiber layers together to leave behind clean material. A July 2020 article published by Boeing’s environmental division estimates that the partnership is reducing solid waste sent to the landfill by more than one million pounds per year across the selected sites.
Hadigheh said his team has seen some interest and is continuing to advance their patented new carbon recycling method.
“We had some interest from Airbus early in 2020 before the pandemic hit their market. Since then, we have not heard from them which is totally understandable in regards to their financial situation,” Hadigheh said.
At the next stage of their research, Hadigheh will focus on further investigation on effective pyrolysis and oxidation of FRP composite panels. This will make it possible to carry out mechanical tests on rCFs, as well as remanufactured composites made of rCF.