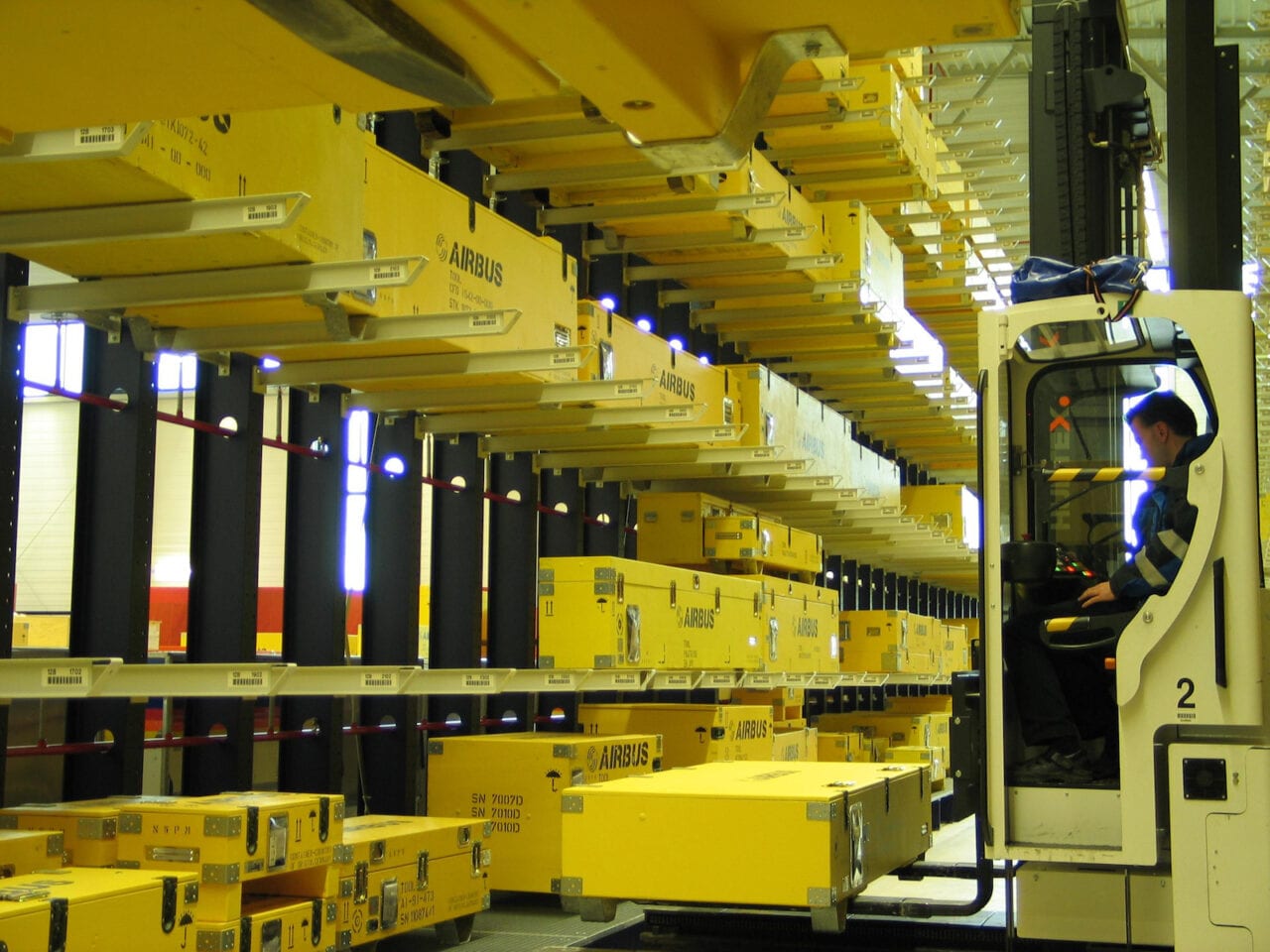
A picture of Airbus Services subsidiary Satair’s tooling facility in Hamburg, where it is supplying what is believed to be the first certified additively manufactured part to fly on an in-service commercial airliner. (Satair)
3-D printing is no longer a new or innovative technology for the largest manufacturers in aerospace who have been creating solid objects from digital files for more than a decade, but what’s happening across the industry now is a massive expansion in the number of use cases where additive can replace conventional methods of manufacturing commercial and military aircraft parts at lower costs, faster lead times and with more digitally flexible design and development methods.
As just one major recently highlighted example in a year that has included a number of aerospace industry additive manufacturing advancements, Airbus Services subsidiary Satair supplied what it “believes,” according to an Oct. 27 press release, to be the first additively manufactured certified metal printed flying spare part to an un-disclosed U.S. airline that operates a fleet of Airbus A320 current engine option (A320ceo) aircraft.
This particular advancement represents a growing trend where major OEMs like Airbus are able to 3D print older aircraft parts using new materials at lower costs and faster lead times. The first passenger-carrying A320ceo entered into service in April 1988 and 22 years later Satair has found a way to replace the aircraft’s conventionally manufactured part wingtip fences that are used as a method for addressing wingtip vortices that can develop below the wing.
According to Satair, the wingtip fences on the A320ceo are installed in four different positions – starboard, port, upper, and lower. These parts are A320ceo specific and no longer in production, and the sole spare parts supplier for the cast version of the part recently experienced difficulties supplying it which started to lead to a regular loss of the molds used to hold the wingtip fences in place by operators.
“Without the part, the aircraft cannot be operated,” Felix Hammerschmidt, head of additive manufacturing solutions for Satair told Aviation Today in an emailed statement.
“As there was an issue with the conventional supplier there was a risk of a future supply shortage which could have led to the grounding of an aircraft. By switching the part to additive manufacturing the issue was solved and the supply is secured for decades to come,” he added.
When Airbus Services received an order for the A320ceo replacement parts and their AOG procurement department was unable to find a supplier, they turned to their additive manufacturing division’s RapidSpares design offices. There, a new certification process was used to re-certify the cast version of the part within five weeks, and adapt it to titanium, a commonly used additive manufacturing material that has repeatedly demonstrated the ability to meet international airworthiness certification regulations for additively manufactured aircraft materials.
Hammerschmidt said the lead time for certification of the wingtip fences could be reduced even further in the future as the technology becomes increasingly standardized.
“The part is believed to be the first metal application for after-sales reasons only – in serial production, there are already plenty of metal parts across different programs and especially engines,” Hammerschmidt said. “The wingtip fences are manufactured in Titanium by the additive manufacturing process called Laser Powder Bed Fusion (L-PBF) which produces parts layer by layer from a very fine metal powder using a high-power laser to melt the material. You end up with a fully dense metal part.”
By spreading the fixed costs such as the setup of their L-PBF machine and powder layup across more parts, the AM division of Airbus can drive down the cost per part of developing wingtip fences and other parts by printing a full four-part wingtip fence shipset in one run, the company’s head of AM solutions said.
Airbus is one of many aerospace companies exploiting the use of additive manufacturing for different purposes, especially replacing conventional manufacturing with an additive to lower costs. Other recent examples include Honeywell Aerospace, which marked a major additive manufacturing technical milestone in August, by creating what the company described as the “first certified, flight-critical engine part using additive manufacturing, commonly known as 3D printing,” in an Aug. 19 press release.
The part is further described by Honeywell as the “#4/5 bearing housing, is currently in production and was installed on an in-service engine.” Dassault’s Falcon 20G maritime patrol aircraft, used by the French Navy for patrol and search and rescue missions, operate ATF3-6 turbofan engines that use the additively manufactured bearing housing.
Elsewhere in the industry, Boeing’s 777X is another example of how far 3-D printing has come in the aerospace industry. The 777X, which completed its first test flight on Jan. 25 and is projected to enter into service by 2022, features two GE Aviation’s GE9X engines each with 300 3D printed parts. GE9X features 3D printed fuel nozzles, temperature sensors, heat exchanges, and low-pressure turbine blades are among the many parts made by GE Aviation’s Additive Technology Center, which added 27 Arcam electron beam melting (EBM) machines to its Ohio facility last year to titanium alumni blades for the 777X engine.

Low pressure turbine (LTP) blades 3D-printed from titanium aluminide (TiAl) for the GE9X engine. Of the seven components and 304 parts being additively manufactured for the GE9X, all except the LPT blades and the heat exchanger are cobalt chromium alloy parts. (GE Aviation)
Aerospace companies are also increasingly adopting new digital tools to accelerate the design and data gathering development phase when considering the use of additive manufacturing for specific parts, Aaron Frankel, Vice President of Siemens’ additive manufacturing software program told Aviation Today.
Most of the 3D-printed parts actually manufactured by Siemens are for their own products used in the energy, medical, and mobility industries, according to Frankel. However, companies like Materials Solutions, Sintavia, and Morf3d that directly 3D-print parts for aerospace companies are using their additive development software.
“Our software is being used to design parts from standard brackets, to airframe components, to jet engine components and systems. When it comes to additive, aerospace companies are utilizing the technology for some very innovative solutions to complex problems. These innovations are enabled by the way that additive allows for the manufacturing of very complex geometries with the pinpoint precision necessary in the aerospace industry,” Frankel said.
Siemens is mainly seeing demand for additive manufacturing software services by companies based in the U.S. and Europe, Frankel added. These companies are producing aircraft engines, satellites, space vehicles, and military equipment.
“Since AM-specific geometries like lattice structures and topology optimized structures can be used for weight reduction, this leads to reduced environmental impact, and improved ROI from these activities,” Frankel said. “For example, when 1 pound of weight costs as much as $10,000 to launch into space, every bit of weight saved turns into large cost savings. When you also consider the lower fuel requirements, and therefore the improved environmental impact from reducing weight, you can see how the adoption of additives can be very attractive for companies who produce products like space vehicles and satellites.
A $1 million contract issued by the U.S. Air Force to New Mexico-based additive manufacturing systems supplier Optomec on Sept. 2 represents another new use case for old aircraft parts, repairing them. Under the contract, Optomec will use a process called Directed Energy Position (DED), “in which a highly concentrated stream of metal powder is jetted into a molten pool created by the focus of a laser beam,” the company said in a Sept. 2 press release.
By precisely controlling the melt pool and the powder flow, a high-performance metal structure is built up, either in the form of a fully printed part or as a local deposit onto an existing component to repair it. According to Optomec, their LENS technology enables the new repair method and will be used to process thousands of repairs a year.
Airlines are also looking at how they can use 3-D printing to lower the cost of replacement parts, through internal investments and partnerships. Etihad Aviation Group’s maintenance, repair, and overhaul (MRO) division opened the first additive manufacturing facility with design and production approval from the European Aviation Safety Agency (EASA) in November 2019 after becoming the first Middle Eastern airline to use a certified 3D-printed aircraft interior monitor frame in 2017.
In February, the airline formed a partnership with BigRep that will install the company’s BigRep Edge 3D printer at its MRO facility in Abu Dhabi to print both flying and non-flying parts on-demand. Several months prior to Etihad’s 3D printer acquisition, in December 2019, British Airways began researching the use of 3D-printing for up to 10 aircraft spare parts that the airline believes could be developed using 3D-printing in the near future. These include tray tables, windows, in-flight entertainment screens and flight deck switches.
In the future, Airbus’ head of AM, Hammerschmidt, believes that within the next few years there will be more opportunities to 3D-print metal technologies in the way they’re using additive for the A320ceo wingtip fences.
“Applications today and in the future are widespread,” Hammerschmidt said. “Additive offers the potential to reduce weight and improve part functionality, for example, the reduced pressure drop in hydraulic systems or improved efficiency of engines. The development of greener aircraft could also benefit from the possibilities that additive manufacturing offers as some technical solutions might be so complex that they cannot be manufactured by conventional machining.”