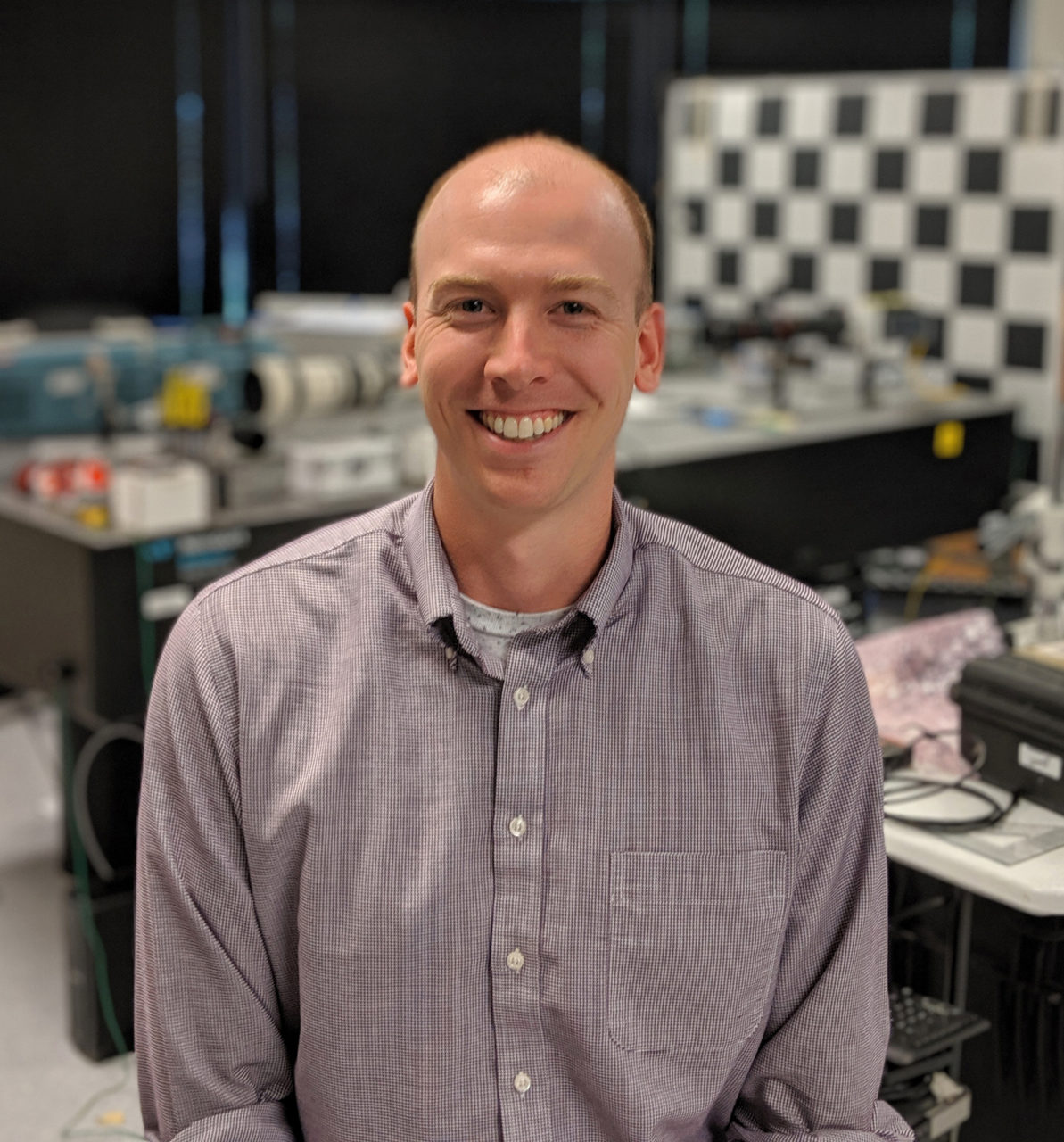
Logos Technologies engineer Zach Currier. (Zach Currier)
Zach Currier likes working at a small company like sensor-focused Logos Technologies, where he’s a mechanical engineer and hardware lead. Formal meetings are infrequent, and he can just pop into the office of a co-worker for an impromptu “whiteboard session to get through stuff” when necessary.
Even better, a number of those coworkers are friends from school. While studying physics at Maine’s Colby College, Currier exploited an agreement with nearby Dartmouth to take classes in its engineering department, which the smaller Colby didn’t have. He found he liked engineering better — “physics got a little too theoretical” for him — and parlayed the relationship between the schools into a Dartmouth master’s in engineering after graduation.
Now he oversees the BlackKite program for Logos Technologies, an electro-optical infrared wide-area motion imagery (EO/IR WAMI) sensor pod for manned and unmanned aircraft.
Currier told AVI about BlackKite’s status and what it’s like to rebuild a broken-down car and enter it into a 24-hour race.
What do you do as an engineer for Logos?
We’re a pretty small company, so I am lucky enough to get to work on multiple different things. One morning, I might be focusing on this Blackkite project, for example. We do a lot of computer-aided design.
We use [Dassault Systèmes’ software] SolidWorks here. So, I might be completely sitting at the computer all day but usually not. We have really good lab facilities, so we do a lot of working on optics, spend time calibrating cameras, getting systems like that setup. And then, from there, we take that camera out and build it into a physical system.
We also have a really good machine shop. A lot of the parts that we design, we’ll send out to machine shops, but we have the capability to — if the timeline doesn’t allow us to send stuff out to machine shops, we can make things in-house here, or if things don’t quite fit together, we can touch them up. So, I might be designing a part in the lab or on my computer here, and then I can run down the street, throw it on our machines and make it in the shop as well.
I get to do a lot of testing, which is cool. Right now, we have a laser set up where we can do testing of some of our mirror systems. We like to use mirrors to steer things around. We’re characterizing the stability of one of our mirror systems right now by shining a laser off it and using high-speed cameras that can do measurements.
What is the most interesting thing you get to work on?
I mentioned this BlackKite project that I’m working on. We have a product called RedKite, which is our daytime wide-area motion imagery – WAMI – payload, that comes in two forms. We have it in a form that is a pod that flies on manned aircraft or some wing-mounted UAV systems. We also have [the RedKite-I] form-factor that [fits in an Insitu] Integrator UAV under the center bay of the aircraft. That’s one thing I helped with a little bit and now, we’re working on BlackKite, which is our nighttime IR version of that same system.
Effectively, we are working to accomplish the same mission. We have to do it in a little different way, but the conops would be the same there.

Logos Technologies’ RedKite WAMI sensor on a Stemme S15 glider. (Logos)
What’s so interesting about the way you’re accomplishing the mission with BlackKite?
We’ve been working on it for a long time. When I started here, we did some engineering development work on it, proof-of-concept stuff. It was a good foot in the door to try things out. We did a lot of truck testing; it’s a tough controls problem.
This one of these projects where it’s kind of been on and off the shelf. It was an internally funded project, so we’d get some money and then, when that money ran out, we put on the shelf. We’ve slowly been building and we finally put it into an integrator form factor, which has been a big goal of mine — to get it to a point where it starts to look like the payload that’s going to eventually go on a UAV. Just a month ago or so, we got it up in the air and collected data in that form factor, which is a big step for us.
We’ve flown development units before of this same system, but this has got the best- looking new one, the closest to our eventual product state.
What’s the product roadmap going forward for BlackKite?
I don’t know of actual release dates for when we get to a final product state, but we have a version of the system that we need to do embedded processing on it. That’s a big step for us, to take our payloads, not only collected data but do all the processing and rendering and send it to the ground in real-time. The next step for us on that product is to take it from its current state and then just put that inside. I think later this summer we probably will fly again and it will be close to that state. We have some outside money that we are looking to get going here soon, and that’ll be a real surge of energy to push this to the finish line.
Switching gears, what do you do outside of work?
Growing up in Vermont, I have quite a bit of outdoor tendencies. like to run, play golf, play volleyball. I love to ski. I can’t really do that all year round here but try to take as many trips as possible, either back home to Vermont or head out West.
There’s a couple of engineers here, for a while we had a race-car team that we started. We raced in a league called “24 Hours of LeMons,” where you buy a lemon, you’d have to buy a car for under $500 and turn it into a race-car. Basically, it’s a play on the race in Le Mans, France, where you do as many laps as you can in 24 hours. The goal of this race is to keep your car alive for as long as possible. We got to use our engineering skills, outside the office, but then you also get done and do some wheel-to-wheel racing, which is pretty entertaining.

Zach Currier driving his team’s rebuilt Volkswagon in the “24 Hours of LeMon” race. (Zach Currier)
Hold on, this is great, I need some more information here. How did you guys usually do? Were there any specific techniques you used?
Yeah. So, we ended up actually buying our car off another coworker. It was a Volvo 815 luxury family sedan. We tore all of the seats and everything out. Took as much weight out of it as we could. The clutch was bad, so we had to tear the engine apart and rebuild part of that, put a roll cage in it, put racing seats in.
Testing a race-car like that is basically impossible because we don’t want to pay for track time. So all of our testing happened at races at the time the races were gaining in popularity, so [it was] maybe as a 200 car field on a road race track. So, you’re not in bumper to bumper traffic, but you’re pretty much right next to someone for as long as — we’d drive in about hour stints or so. It’s a family sedan, so maybe we’d get up to a hundred miles an hour if you’re really horsing it. It’s definitely a little bit of a tongue-in-cheek race league, but the racing itself is pretty real.
Is winning about attrition? Are cars just falling apart on the track around you?
Yeah. You kind of theme your car. Our car as an IKEA theme, so we covered it in wood-colored contact paper. It kind of looked like a coffee table. There are different levels of the cars — some people bring old BMWs, and the judges don’t like that. They’re there to race really fast. And then there are other cars that are literally spewing oil and falling apart. They make it a couple of laps, and the engine explodes, and they have to tear it apart and build it while they’re at the racetrack. That’s what the judges are looking for. We were kind of a happy medium.
Some of the engineers I talk to try to turn that part of their nature off when they aren’t working. It doesn’t sound like you do.
That’s a great example of a way that it leads right into it. I would say I don’t try to curtail it. I like to get my hands dirty and try to build things.
Obviously, you can’t build a car in an apartment, but do you do other things at home?
I don’t have a fully automated home like some people, but in terms of fixing things up — If the garbage disposal breaks, I don’t want to call anyone. I’d rather buy the part or fix it myself.
This interview was edited and condensed for length and clarity.
Editorial Note: In an effort to show a behind-the-scenes look at the engineers building new aircraft, networks and embedded systems, Avionics International (AVI) is looking to profile aerospace engineers from around the industry on a weekly basis.
We also want to show the next generation of engineers how they can get into a career as an aerospace engineer and what the day to day life of an aerospace engineer looks like. Have a suggestion for who we should profile next? Email the author of this article to let us know!
Update, 7/15: Changed to reflect the proper capitalization of “BlackKite” and clarify the RedKite’s use on Insitu’s Integrator.