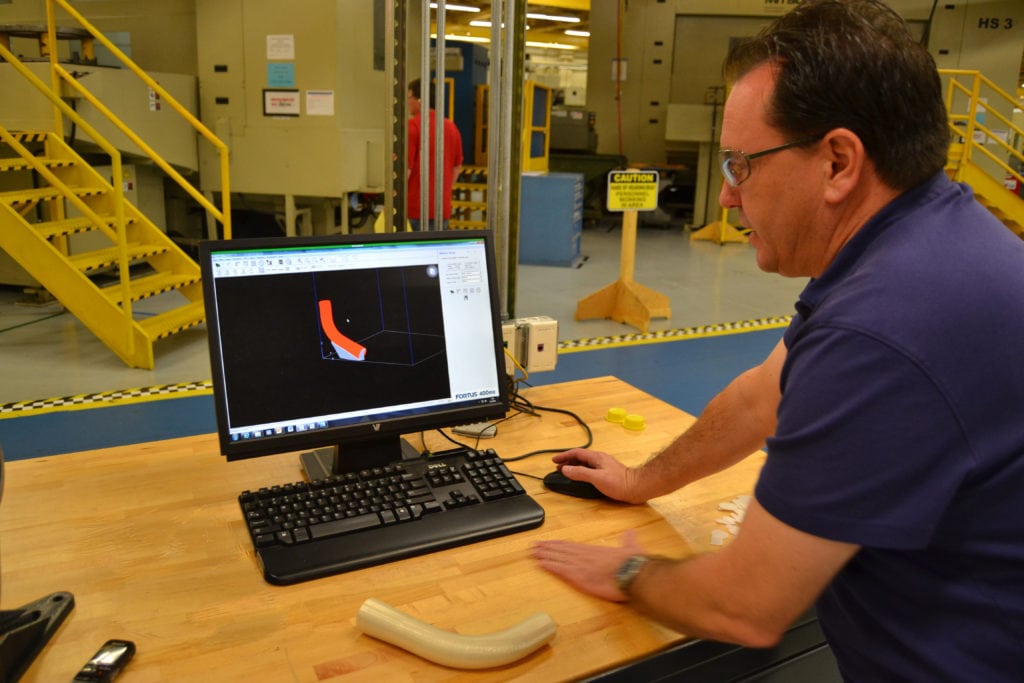
Randy Meeker, a Fleet Readiness Center Southeast tooling designer, shows how a piece of environmental duct for a T-44 Pegasus was designed and created with a 3D printer in the facility’s manufacturing department. Photo courtesy of the U.S. Navy
If an original equipment manufacturer is out of a part that is needed in a maintenance, repair and overhaul task, 3D printing could be a solution. At least that’s what Fleet Readiness Center Southeast (FRCSE) decided. The center says it successfully 3D-printed its first component: a replica of Ultum 1085 air duct tubing.
“This is an awesome milestone for our facility,” said FRCSE Commanding Officer Capt. Chuck Stuart. “It shows the innovative approaches our artisans and engineers incorporate to help support the U.S. military every day.”
The fleet readiness center has been in possession of an operational 3D printer since June 2014. So far, it had been used for making parts for support equipment. The center says this is the first time the printer has been used for an actual aircraft component. When an engineer found that Raytheon had exhausted its supply of a piece of air duct used to circulate air throughout the cockpit of a T-44 Pegasus, he asked the center for help. Randy Meeker, a tooling maker at the facility who runs the 3D printer, decided it could either develop a product similar to the part, or 3D print it. Cost analysis showed 3D printing would be most efficient, for quality as well. Meeker was able to improve the design. Originally two pieces with a flange, the new printed piece was a singular component.
“There is a lot of responsibility on the engineer for these parts that are actually used in aircraft,” Meeker said. “It’s a whole new world of technology, and it’s their responsibility to make sure it can be used safely. That’s why this particular project was a good first candidate because it’s not a flight-critical part, but it’s a step forward in incorporating 3D-printed parts into aircraft.”