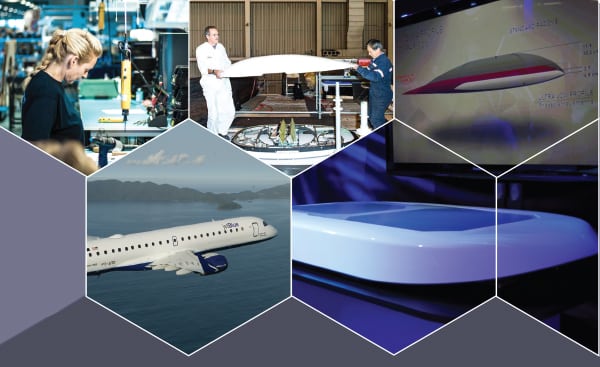
The aircraft connectivity market is in the midst of a full-fledged upswing, as passengers demand constant contact with the outside world, even at 30,000 feet. Gogo alone provides connectivity services to nearly 2,000 commercial aircraft and 7,000 business jets. This equipage is only rising, enabling more efficient cockpit operations as well as a passenger-pleasing amenity, which is a near necessity in the business aviation market.
“It is becoming essential for … travelers to have access to high quality, low-cost voice calling and full complement data services, supporting the use of Wi-Fi enabled devices, such as laptops and smart phones,” says Willem Kasselman, marketing director at Cobham Satcom, noting that fleet owners report that business flyers often will not fly in an aircraft that isn’t Wi-Fi-enabled.
Carrying this connected revolution is, of course, the antenna. Avionics Magazine’s 2014 antenna market survey found that more than 45 percent of respondents were using antennas for connectivity purposes, but Todd Hill, director of technical operations at Panasonic Avionics, finds that while connectivity drives demand, it doesn’t necessarily drive sales. And it isn’t just connectivity driving the demand for new antenna technology, with more than 83 percent of respondents to our antenna survey noting that upcoming mandates would increase the need for higher-performance antennas on their aircraft.
Capitalizing on Connectivity
“[Connectivity] is definitely driving the demand,” says Hill of the antenna industry. Driving demand, however, isn’t the same as driving sales. “When it comes to quantity, it’s really hard for us to drive. A single Best Buy will move more product than we move in a year,” He explains. “What it is doing is driving the technology faster.” The antenna’s role is changing. Where military users previously dominated the customer roster, according to Hill, commercial applications are now moving the devices into the air transport arena. And with a changing customer comes a shifting price point.
“For military needs they’ll spare no expense. But for the commercial market, while everyone wants Internet on an airplane, they only want it at a certain price,” says Hill. Technological advancements, such as the integration of digital and RF circuits, allow for a more cost-effective solution for commercial customers with tighter wallets, and Panasonic Avionics is looking to power some of this burgeoning tech. The company has recently partnered with Boeing Network & Space Systems to develop a broadband, electronically steered phased array antenna for commercial airliners that will deliver in-flight Wi-Fi through Panasonic’s eXconnect service. The lightweight, low-drag antenna promises to save the typical Boeing 737 operator $65,000 annually at current fuel prices, according to Hill, due to its low profile design.
Paul Geery, vice president of C3 Solutions for Boeing Network & Space Systems, says the flight-test program is expected to happen in the 2016 timeframe. Boeing will solidify the design this year, and wants to finalize the configurations from an overall system and packaging perspective including the details between the on-board systems and the Panasonic network.
In terms of whether this will ultimately become a line-fit option for airlines in the future, Geery says Panasonic will be the driver here. “I would imagine there would be a push from the airlines to make this a line-fit option. But, that has not been decided yet,” he says. He admits it will likely start as a retrofit, and depending on customer demand, other options could be explored.
While this antenna offering from Boeing and Panasonic is purely for an entrance into the commercial airlines business for in-flight entertainment, and not intended to provide satellite connectivity to information in the cockpit or with any of the safety critical systems that are embedded in the airplane, it could ultimately develop in the future.
“Of course with this kind of technology you can imagine that, over time, there might be a desire to provide a better wideband connectivity to those kinds of systems. But, at this point, we haven’t started working anything of a serious nature to have this kind of connectivity,” says Geery. “There are reasons for that. There are things that have to be done that have to separate and protect the avionics systems on the aircraft. You have to make sure there are no safety issues. You have to work those things up through the FAA. We just haven’t started this process at this point.”
Meanwhile, In-Flight Connectivity (IFC) giant Gogo is also making the most of new designs to further connectivity with its high throughput 2Ku dual link antenna. The dual-antenna layout enables a ground-to-orbit solution as one transmits an upward, receive-only link for satellite communications (satcom), while the other provides a downward, return link. When the antenna becomes available in 2017, it will take advantage of spotbeam technology to deliver speeds of up to 70 Mbps to airlines such as Aeromexico, which has already committed to the connectivity solution. The antenna also stands 4.5 inches tall, reducing aircraft drag.
“2Ku’s performance benefits will be even more dramatic in tropical regions where other satellite solutions degrade significantly due to restrictions associated with operating at high skew angles,” says Niels Steenstrup, senior vice president of international sales at Gogo. He disagrees, however, that connectivity is driving demand.
“I think it’s the other way around,” Steenstrup says. “You see antenna technology influencing how we are able to deliver better and more consistent connectivity solutions.”
Spectrum Speculation Drives Design
 |
Panasonic broadband connectivity antenna. Photo courtesy of Panasonic. |
These improved connectivity solutions include more efficient ways to deliver spectrum. Ka and Ku band have yet to be approved for Air Traffic Control (ATC) applications, leaving L band to serve the cockpit in the foreseeable future. This leaves the high speed Ka and Ku-band to battle it out in the cabin — a battle that will ultimately come down to cost benefit, and not performance, as one might think, as it ranked last when respondents to our 2014 antenna market survey were asked about the most important aspect when purchasing an antenna.
“Airlines seldom express any preference for spectrum; it is about cost benefit of the system,” said Kasselman. “For pure cabin and perhaps limited aircraft operational connectivity, the choice between Ku and Ka will be based on cost, throughput, coverage and any other benefits that the service provider may be able to offer,” he adds noting that L-band solutions are relatively mature and the required aperture, side-lobe suppression and cross polarization protection requirements make it so that the size cannot be reduced any further.
“As you move up in Ka band from L band, which is a factor of 10 higher, one of the other things that it does is it drives, in some cases, totally different antenna technologies,” says John Broughton, director of marketing and product management at Honeywell Aerospace. “The reason for this is that the things that work at lower frequencies don’t necessarily work at higher frequencies. At L-band, there’s a range of antenna technologies that provide different solutions depending on the application and the type of aircraft.”
These technologies include mechanically steered antennas, which tend to be used on business jets sitting on top of the tail, while phased array antennas, where electronics steer the antenna, tend to sit on top of the fuselage and are the solution of choice for larger airframes. Electronically steered phased array antennas don’t require any movement and therefore tend to be lower profile, less visible and reduce drag. The downside, however, is that they cannot see down to lower elevation angles, limiting use to aircraft that fly routes closer to the equator and outside the Arctic Circle.
“Low-profile antennas are somewhat limited in how close to the horizon they can look. So they are not the best choice for planes that fly the polar routes. The airline’s route structure will determine if the antenna is a good fit for their wide-body fleet,” Hill says. Although it should be noted that the phased array does cover a large percentage of routes — a reported 99 percent, according to Hill. Next Generation Antennas
ARINC 792, a standard that the Airlines Engineering Electronic Committee (AEEC) Ku/Ka-Band Satellite Subcommittee is developing to reduce satellite communications equipment design and installation costs for airlines, is shaping up the next generation of antenna technology. ARINC 792 will also accommodate for larger and more complex apertures and dual antenna designs coming into the market, such as Gogo’s 2Ku antenna, says Peter Lemme, chairman of the Ku/Ka-Band Satellite Subcommittee, founder of JetWayNet and a former Boeing engineer.
“Right now we are working on project paper 792, which eventually will become ARINC 792,” said Lemme. “It is intended to be the second generation antenna design, whereas ARINC 791, which we began in 2008, has sort of lived to maturity so we’re moving on to what we think are updated logical evolutions in technology and also a major change in the way we specify the installation of the antenna itself to try to get away from creating barriers to commonality or interchangeability.”
ARINC 791 defines antennas into two major sub assemblies: one part being the antenna and the other being the modem and Ethernet switch which provide the digital spark. Under 792 though, the committee wants to provide a standard set up to accommodate for market diversity.
“ARINC 792 is attempting to start from a different direction to find a way to specify the antenna without getting into the attachment to the airplane,” said Lemme. “If you think of the antenna, there is the RF piece [and] the aperture that sends the signal, and that sort of stands on four legs and so we just want to talk about where do we want to attach those four legs. How that structure gets attached to the airplane is no longer our concern. That allows anybody to build that supporting structure to their satisfaction but use the same four mounting holes to latch the antenna down so you don’t have to design the antenna differently from one airplane to the next. That is the fundamental design change we are trying to do from 791 to 792.”
Stakeholders that are contributing to the new standard include antenna suppliers such as Kymeta, Gogo, ThinKom, Nordam, and W.L. Gore. Boeing and Bombardier have committed resources and Delta and Norwegian Air Shuttle are also involved. “The natural movement in technology is that whatever it took to build it before can be built smaller, lighter and cheaper with less power today. That’s definitely true in RF electronics, and the big one we’re focused on is all the stuff that has to drive the beams,” said Lemme. “When you do a satcom installation you have to consider the fact that you’re plugging equipment in several places inside the airplane, and you’re bolting down this assembly on the outside. You have to go through an alignment and calibration process once you put everything in place to make sure the antenna is pointed in the right direction and the power levels are optimized. If you don’t, you can end up not getting enough power or you can mispoint and those are both bad things. That’s a cumbersome process we want to automate that as much as possible.”