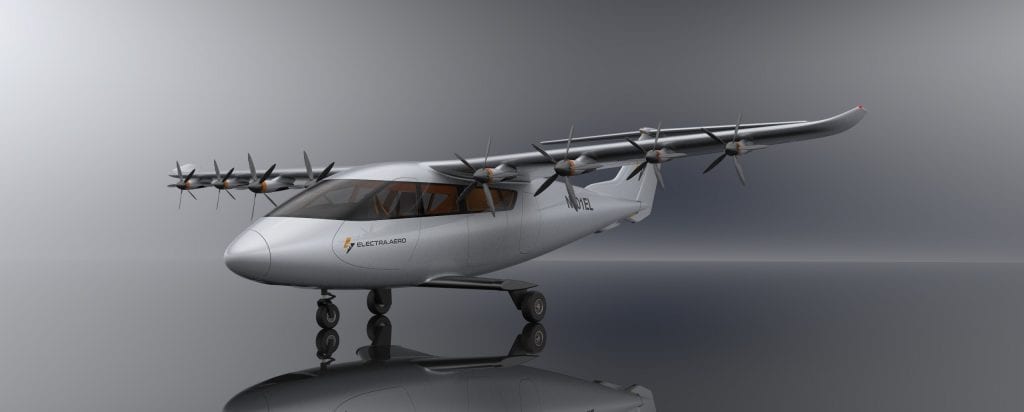
Electra claims its ultra-short takeoff and landing aircraft can deliver nearly triple the payload capacity, an order of magnitude longer ranges, and less than half the operating costs. (Electra)
The Agility Prime program from the U.S. Air Force has invested in multiple electric vertical takeoff and landing (eVTOL) aircraft and now it is investing in a new type of flying car, an electric ultra-short takeoff and landing (eSTOL) aircraft through a partnership with Electra.aero.
The Air Force awarded Electra a $1.5 million direct-to-phase II small business innovation research (SBIR) contract with a 15-month performance period, Ben Marchionna, director of technology and innovation at Electra told Avionics International via email. Electra plans to complete the work for this contract by July 2022.
“Agility Prime is excited to partner with Electra on their recent Phase II SBIR contract award,” Agility Prime’s Deputy Lead, Major John “Wasp” Tekell said in a statement. “We look forward to exploring the unique capabilities of this design while continuing to accelerate the electric aviation industry.”
An eSTOL aircraft differs from eVTOLs because eSTOLs use electric propulsion combined with a technique called blown lift to takeoff over very short distances.
“eVTOLs use electric propulsion to takeoff and land vertically – many of these concepts then transition from vertical flight to forward flight with a wing providing the lift once in cruise,” Marchionna said. “Vertical flight requires significantly more power, resulting in an enormous payload, range, and cost penalty. eSTOLs use electric propulsion and an aerodynamic technique called blown lift to takeoff over distances as short as 100 feet. This provides eSTOL aircraft access to many of the same urban air mobility markets.”
The blown lift technique utilizes the aircraft’s wings and propellers to push large amounts of air over the aircraft’s wings and push the air downwards, Marchionna said.
“Blown lift is an aerodynamic technique that tricks the wing into thinking its much larger than it really is,” Marchionna said. “Propellers are typically used for thrust and the wing is used to generate lift. Blown lift uses the propellers to also blow significant amounts of air over large wing flaps that deflect the air downwards. This can be done very efficiently across the entire span of the wing with distributed electric propulsion systems. The technique has been used for nearly 75 years, with extensive research, flight testing, and operations by NASA and the USAF in the 1960s and 70s, but the advent of distributed electric propulsion now makes blown lift practical again.”
Electra’s eSTOL will also use a custom battery system that can be charged mid-air, Marchinonna said. Recharging the battery mid-air will allow Electra’s aircraft to conduct missions over longer distances.
Electra claims that its eSTOL will offer more payload capacity, longer ranges, and fewer operating costs than eVTOL aircraft.
“The improved payload, range, and operating cost are not compared to any specific eVTOL platform – rather, these advantages come from the fundamental physics,” Marchinonna said. “Taking off vertically, even if only for a few seconds before transitioning to wing-borne lift, requires big compromises in performance and safety. An eSTOL requires one quarter the power of an eVTOL to lift the same payload.”
Electra’s aircraft will have a capacity of seven passengers and one pilot with a range of 500 miles, Marchinonna said.
Electra has completed the sub-scale testing of its eSTOL and is now building a two-seat technology demonstrator, Marchinonna said. They will begin ground testing this year and flight testing in 2022. By 2026, Electra is expecting to have its aircraft certified by the Federal Aviation Administration under Part 23.