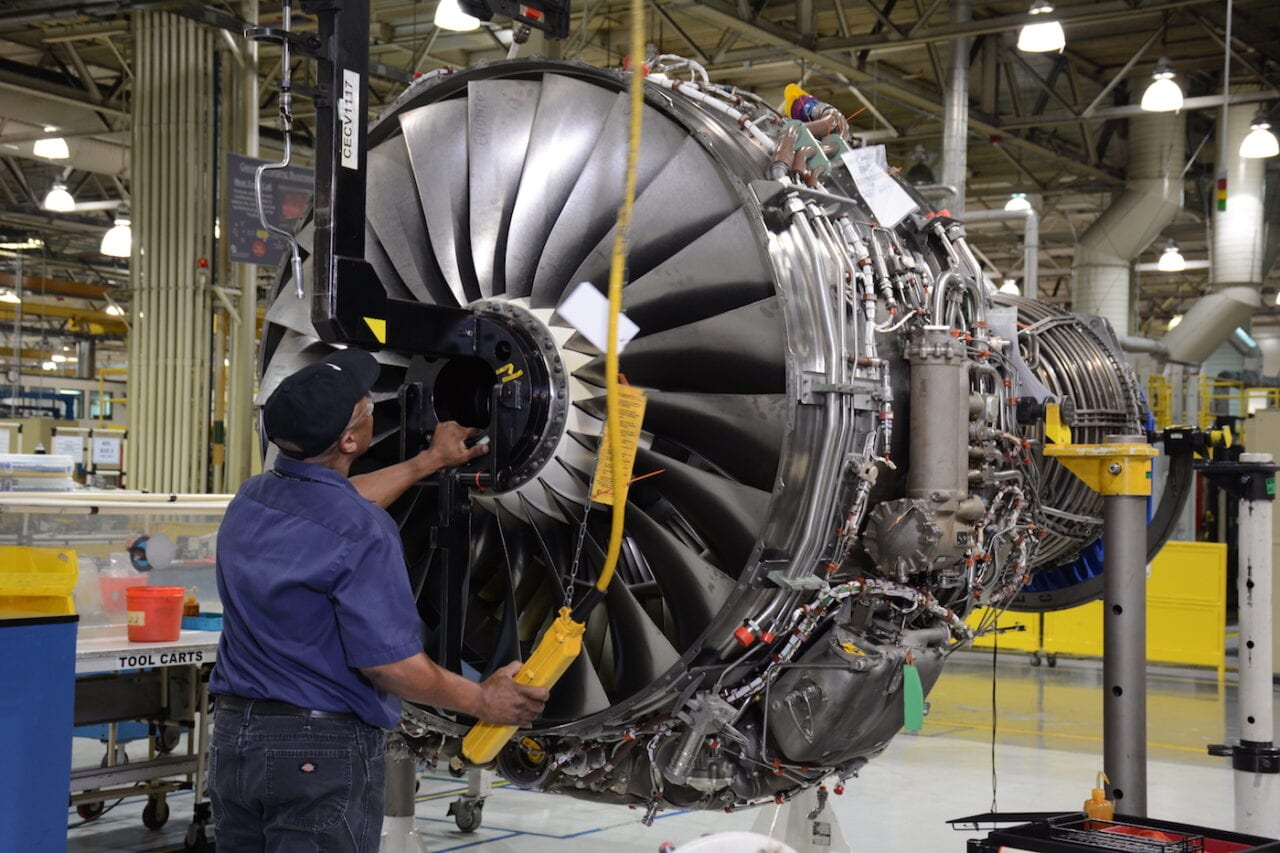
The aerospace supply chain is starting to embrace the concept of “Industry 4.0” in various ways. Major OEMs such as Pratt & Whitney, whose engine overhaul facility is shown here, are working with suppliers to use digital transformation to eliminate bottlenecks. (Pratt & Whitney)
Inside aerospace manufacturing facilities across the globe, many companies are using digital transformation technologies to connect their most critical physical assets to information sharing systems that can provide every customer and supplier stakeholder across the supply chain ecosystem a digital view status, quality, schedules and other key performance indicators (KPIs). This concept has come to be known across all major manufacturing industries as “Industry 4.0.”
According to Deloitte, Industry 4.0 is the “Fourth Industrial Revolution” or the “creation of a digital manufacturing enterprise that is not only interconnected but also communicates, analyzes, and uses information to drive further intelligent action back in the physical world.”
Three platforms that most aerospace suppliers use today are key to establishing the type of digital data thread necessary to help companies embrace Industry 4.0.
- Enterprise Resource Planning (ERP)
- Product Lifecycle Management (PLM)
- Manufacturing Executing Systems (MES)
“Lockheed looks at Industry 4.0 as the fourth industrial revolution, we look at it as the revolution of data, we’re trying to integrate data from floor systems from ERP PLM MES systems and figure out how we take all that data in all our systems and use it,” Don Kinard, a senior fellow for Lockheed Martin Aeronautics said during the July 23 “Industry 4.0 for Aerospace Manufacturing in 2020: Impact, Challenges and Best Practices,” webcast hosted by nonprofit manufacturing association SME.
Kinard referenced the F-35 as an example of a program where Lockheed has embraced Industry 4.0 technologies for several years, including the use of “model-based” digital data threads to influence the program’s planning phase for managing manufacturing operational schedules. Lockheed Martin’s path toward its current establishment of more digital data threads, he said, includes the use of IoT sensors attached to machines to help collect data about those machines and give more people across their enterprise an on-the-manufacturing floor view of the status of critical assets, ranging from raw materials to machine components and quality inspection testing.
“To me, industry 4.0 is the enterprise view of the way we do business and how we get everything together,” Kinard said.
Suppliers can embrace more Industry 4.0-style digital data threads that improve workflows and KPIs by deploying the tools and infrastructure necessary to enable such concepts, and companies are ready to supply manufacturers with technologies that enable digital transformation internally and externally in a multitude of ways. Mindbreeze, for example, is an Austrian-based provider of a software-based insight engine capable of taking data from a wide variety of sources and populating it to relevant workers in actionable formats. Their aviation customers include Lufthansa, Siemens and Air France.
IFS, one of the largest suppliers of enterprise resource software to the aerospace manufacturing industry, is another company that has been making digital transformation advancements within its solutions to help enable the aerospace supply chain’s adoption of Industry 4.0. A recent white paper published by IFS, “Enabling A&D Manufacturing Transformation,” notes that the deployment of intelligent assets inside of factories can generate many terabytes of data and that “simply extracting this data — let alone mining it to truly inform business decisions and better take advantage of aftermarket service revenue — is something A&D manufacturing is still trying to master.”
Kanfit Ltd. an Israel-based manufacturer of ready-to-fly composites, metals and hybrid aerostructures is one mid-level aerospace supplier that recently started its digital transformation path and continued to follow it through the pandemic. During the SME webinar, Shachar Fine, executive vice president of Kanfit, said one of the challenges to navigating their digital data sharing relationship with OEMs there are many different ways to plug into the digital threads that are being established.

A visual overview of what the concept of Industry 4.0 looks like according to Deloitte.
“As a supplier to the industry, digitalization is a must, all the large OEMs are going there,” Fine said. “One of the challenges we face with digitalization is each OEM has its own system, as a supplier we need a system that can deal with all of them. That’s one of the biggest challenges we face is integrating with a lot of systems.
Some of the larger names that Kanfit supplies include BAE Systems, Elbit Systems, Rafael Defense Systems and Spirit Aerosystems among others. Upon their January move to a new 11,000 square-foot facility at Tsiporit Industrial Park in Northern Israel, they beta-tested the connection of an artificial intelligence system to bluetooth technology responsible for monitoring the location of engine parts and status of work orders in their factory.
“We took one hundred chips and attached them to various work orders, and let the system run to see what type of feedback it generates. Everyone was really surprised to see on those first one hundred chips the system managed to locate two work orders that went to the wrong workstations, and the system gave warnings to the relevant department managers that the parts they were looking for were in a different place,” Fine said. “That generated some buzz around the factory because parts being misplaced is a huge headache especially when they’re small and can get lost very easily.”
Hanwha Aerospace, a Changwon, South Korea-based supplier of aircraft engine components and systems to Pratt & Whitney, has used digital transformation to embrace Industry 4.0 in different ways regionally. In September 2019, Hanwha completed the purchase of Connecticut-based aviation engine component manufacturer EDAC Technologies, making Ben Adams the president of their new U.S. division.
Adams, during the July 20 FIA Connect 2020 Supply Chain 4.0 webinar said Hanwha has used digitalization to drive 30 percent annual growth for the last three consecutive years. Their current focus is on optimizing the digital interfacing mechanisms they use with some of their major OEM customers, such as Pratt & Whitney schedule project runs. Further digitizing the process of providing model-based definitions and manufacturing requirements are also a priority.
“Having model based definition right up front speeds up our estimating process, it speeds up fixture design, speeds up our capital acquisition process and making sure we have a really good digital view in terms of what’s going to be required. Model-based definition is huge in terms of our ability to go faster,” Adams said.
Improving what he currently sees as a reliance upon larger OEMs for generating scheduling and other associated workflows is a process Adams sees Industry 4.0 correcting in the future as well.
“We generally rely on Pratt’s systems to receive, schedule and make commitments. I think there’s another element in time that will be created to give them more visibility to outcomes and to enhance our communication, which this is all based on. We’ll see where that goes,” he said.
Pratt & Whitney COO Shane Eddy provided perspective from the other side of Hanwha’s customer-supplier relationship during the same webinar, noting that the COVID-19 pandemic has only accelerated the need for the aerospace industry to embrace Industry 4.0.
Pratt’s current focus is on analyzing data collected from their machines on the manufacturing floor and making that data actionable for planning individual manufacturing projects, Eddy said, while also digitally viewing the status of products being assembled by suppliers like Hanwha.
“The data accumulated from these machines these days is unprecedented,” Eddy said. “So all the ingredients are there for a full digital value stream.”