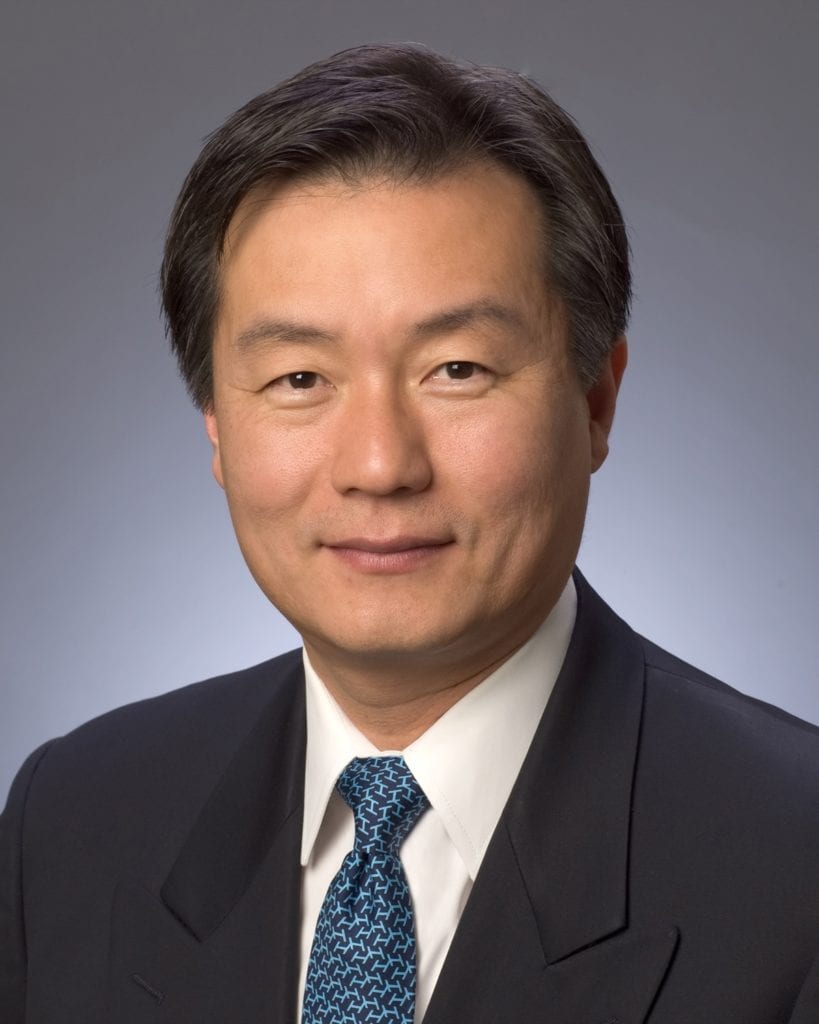
Ike Song, vice president of mission systems for Mercury Systems, discusses embedded technology trends for future commercial, military and urban air mobility aircraft. Photo: Mercury Systems
As the global aerospace and defense industry shifts into the 2020s, embedded systems suppliers are being tasked with supporting certifiable avionics architectures capable of meeting the most stringent versions of DO-178C and DO-254 software and hardware functionality.
Here, Avionics International discusses trends in security requirements, development and changes to embedded processing components with Ike Song, vice president and general manager of Mercury Systems’ mission systems group.
When you look back over the last 3-5-year time range, how have you seen the successful business model for safety critical avionics embedded systems suppliers change and how do you see the business model for Mercury changing going into the 2020s?
We’re close to 99% in terms of on time quality delivery for Airbus and enjoy a similar situation here in the US for the Boeing KC-46A. Our business model is very important and we pride ourselves on providing a commercial business model rather than traditional military business model. So that not only can we co-invest as an aerospace supplier, our speed to market is also faster than the competition.
Similar to Lego-building concept, we provide a significant number of cards as well as the board support package and all of that is already DO-178C and DO-254 safety critical qualified as required for FAA and EASA. That’s already done when we supply that Lego block so to speak, to our customers and then they go on to develop to their needs.
What are some industry trends or disruptions that will impact the business model Mercury uses specifically in supplying embedded technology for the commercial and defense aircraft markets? How will that Lego block keep up with demand?
So I think we have to really segregate the commercial aerospace versus military aerospace and the new emerging urban air mobility markets. If you look at the commercial aerospace market, their lifecycle for any kind of line-replacable unit (LRU) or any kind of electronic is about 20 years. So once an operator or manufacturer is designed into, for example, a 757 or 737NG, they’re not going to change that for next 20 years.
Whereas, on the military side, you have to change every two to seven years mainly because there is a requirement to rapidly add new aircraft capabilities. So you need a more advanced processor. That’s the biggest difference between the commercial and military aerospace markets.
The [urban air mobility] UAM market is actually an even faster cycle time than the military because they’re are a very fragmented market right now and they’re trying various different things. It’s like back in the 1950s and 60s military market where you would actually create an aircraft every six to eight months. That’s what the UAM market reminds of right now.
All three segments have a different cycle timeframe. That means on the commercial aerospace side you have to have enough components to withstand obsolescence issues over 20 years, while also developing new capabilities every three to seven years for military customers and then the UAM market is totally new. And because the UAM market is moving so fast, it will be interesting to see how that market really pushes advancements in new capabilities.
On the UAM market specifically, who would you see as kind of your targeted customers? Is it the traditional aircraft manufacturers or is it a whole new crop of players that are working on new designs?
The UAM market is very interesting because depending on which study that you look at, it could be a $20 trillion market between 2040 to 2050, which is what Morgan Stanley said. Then there’s another study that said it could be a $1 trillion market and then there’s others that say it could just be a flash in the pan type of thing.
My perspective is that I think the UAM market is very similar to the market trend from the early 2000s and the telecom boom; we had the telecom boom followed by the telecom burst. I believe that we’re about to go through a similar situation where in the UAM market: there’s a huge boom now because of a lot of big aerospace companies are investing in it. There’s also a lot of venture capitalists investing in it, so the market is very fragmented.
Lots of dollars are being invested in urban air mobility, or electric vertical takeoff and landing aircraft (eVTOLs). I do think that there’s going to be a burst, just like we had in telecom. After the telecom burst, there were were a few gems that really grew, with the Amazons of the world, and companies like Facebook, Netflix and Google.
I believe that there’s going to be gems just like that which will dominate the UAM area. I don’t know what they are yet. It could be the flight control mechanization. It could be on artificial intelligence and visual navigation or it could be on ground stations. It could be 5G ground stations, but there will be gems and we as a supplier to the UAM market have to be smart about which segmentation that we need to chase to ensure that we have significant market share when the dust settles in the UAM market.

Mercury Systems is a supplier of embedded systems technology to Boeing for its KC-46A program. Photo: Boeing
During an interview with Avionics last year, you noted concepts such as electric vertical takeoff and landing (eVTOL) aircraft as driving the use of the concept of digital convergence, which was described in a Mercury white paper last year. What are some of the key components in terms of memory, circuit boards, connectors or processors that need to make advancements in order to enable the type of functionality being sought by electric air taxi developers?
I think the first thing that they need to figure out is how be able to power the aircraft. It’s just like what happened with Tesla. Once they hit around 250 miles range, it kind of started taking off. eVTOL is going to be similar, where at a certain range, it will start taking off. the battery technology is moving forward. I think the efficiency of aircraft and moving forward.
Also, there’s not enough pilots in the world to, to get trained to have eVTOL become a reality, which means these aircraft are ultimately going to need to be autonomous. I see a lot of convergence with artificial intelligence, EO/IR (Electro-optical/Infrared) cameras with the GPS and IMU combination to make this a reality. When you use AI and when you use a lot of visualization, basically that consumes a lots and lots of memory and a lot of CPU clock speed. Air taxis will also need some graphics and visual navigation, as well as pattern recognition in order to make autonomous piloting a reality for UAM. So I think there’s a couple things that’s happening. I think the visual navigation, on UAM perspective, they’re investing more in that side than the military. Pattern recognition is also really needed for the autonomous piloting.
What type of promise do you see in the Sensor Open Systems Architecture (SOSA) consortium and the overall Modular Open Systems Approach (MOSA) initiatives in making the use of open systems a widespread reality?
SOSA, MOSA and FACE among others, there are a lot of open system architecture standards out there. But fundamentally all of those standards are not really meaningful unless you have very easy way to change your sensors or other equipment. What does it cost to change, any kind of LRU in aircraft, whether it’s military or commercial? How easy is it to change a radio? How easy is it to change [Identity Friend or Foe] IFF? How easy is it to change the radar or [Missile Warning Receiver] MWR or [Radar Warning Receiver] RWR that goes into a fixed or rotary wing aircraft?
And how easy is it from the avionics integrator perspective to make that happen? Even if it’s easy for the integrator to do that, right now the avionics integrators have a monopoly where they are the gatekeeper. So it’s very difficult to change anything without going through the avionics integrator. So, from a Mercury perspective, we don’t believe in vendor lock. We want to ensure in every way possible to create competition. That’s how we can thrive, by competing to supply processors to every kind of sensor vendor and to ensure that they have a fair chance at putting that sensor into an aircraft. And in order to do that, you have to ensure that vendor lock is eliminated where possible, and you also have to find a way to bypass the OFP (Operational Flight Program).
Are there any new or upcoming examples of open systems configurations you can provide that Mercury is supporting today on any in-service commercial or military aircraft applications or operations?
One of the things we’re working on right now is the Apache interoperability station, which is basically a digital twin that the U.S. Army asked us to do. We’re experimenting with the Army to see if there’s any way to bypass the OFP and to inject new sensors or new capabilities into the aircraft. I’m not saying we’re there yet, but we are looking into various ways toward injecting capabilities without touching the OFP.
Do you see those goals differently than the next generation functionality goals of traditional fixed wing commercial and military airplanes?
I think there are certain things that are going to stay constant, like triple redundancy. DO-178, DO-254 DO-326, all of the requirements for the FAA and EASA certification processes, I don’t think that’s going to change. At a fundamental avionics architecture perspective and from a fundamental navigation perspective digital convergence of sensor technology is what can move the commercial UAM market forward.

Mercury expects its Rock-2 multicore design assurance level A certification by March of this year. Photo: Mercury Systems
Now that the ROCK-2 mission computing architecture has a full range of availability of flight safety certification levels, what will Mercury be focusing on in 2020 in terms of supporting avionics manufacturers and systems integrators that use your technology on in-service airplanes?
March of 2020 is when we’re going to get certified for Multicore DAL A for Rock 2. That’s still on schedule. We already have DAL A certification for non-multicore processors. Fundamentally, Power PCs have limited capability relative to the NVIDIAs and the Intels of the world. We need to get NVIDIA and Intel processors to a point where they can meet safety critical avionics certification requirements. They’re not there yet, and we’re working toward that goal. I think that is going to be crucial, to support the level of graphics and processing capabilities needed for the UAM market. Both of those companies though, NVIDIA and Intel are volume players, so they have been heavily focused and invested in supporting ISO 26262 qualification for the automotive market. We need to extend that to the avionics and the future UAM markets, hopefully that can happen in the next three to five years.
Are there any new regulatory initiatives Mercury need to address or industry supply chain changes that will impact Mercury?
On the commercial side, it’s a lot more straightforward because the FAA and EASA came out with the DO-326, which are cybersecurity requirements. On the military side it’s a little bit more difficult to figure out what they want to do because from military perspective, there is cybersecurity as well as anti-tamper requirements. Right now it is very unclear for how they define those as two separate requirements and really there’s no clear requirements coming down from the military side. Someone needs to clarify what those requirements are so that we have a solid target moving forward. Right now, everything is kind of a separate entity, whether it pertains to cybersecurity or anti tampering requirements on the military side.