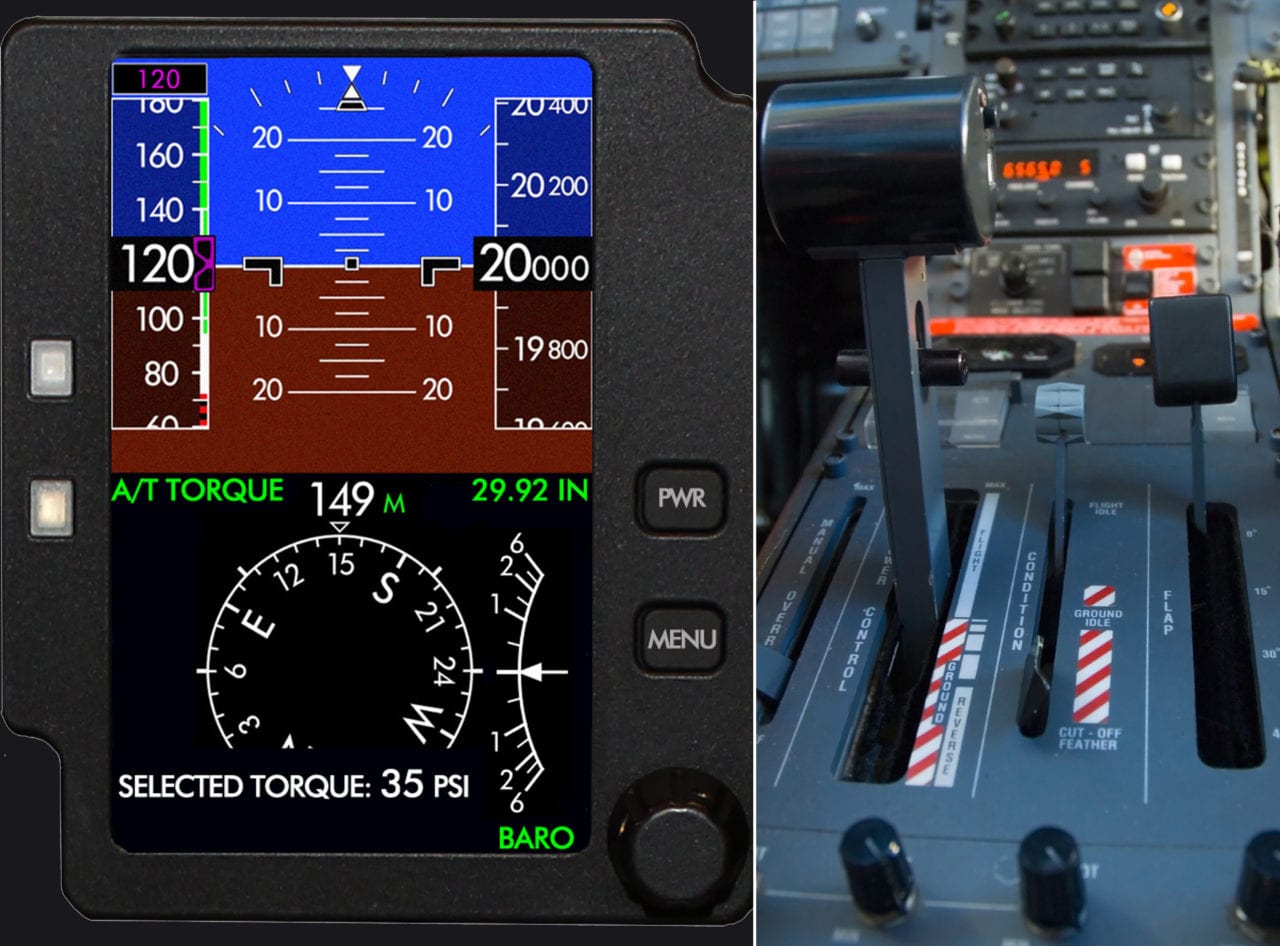
Left: ThrustSense’s integrated standby unit in torque monitoring mode. Right: The throttle quadrant, controlled by the ThrustSense system, both installed on a PC-12. Photos courtesy of ThrustSense
Innovative Solutions & Support (IS&S) is bringing its autothrottle technology from the Pilatus PC12 to the King Air. The company expects the supplemental type certificate (STC) for the Beech King Air B200 to be finished in the first quarter of 2019. After that, the 350 is on deck for later in the year.
IS&S’s ThrustSense autothrottle is in many ways comparable to a full authority digital engine control (FADEC), with one major change — the throttle physically moves, precisely to within a thousandth of an inch, leaving manual control always available to pilots. IS&S’s solution can control airspeed, protect against over-torque or over-temperature, provide minimum controllable velocity (Vmc) mitigation and reproduce many of the other capabilities of a FADEC but in a non-FADEC engine.
“The challenge was the mechanism,” said IS&S CEO Geoffrey Hedrick. “Without that, we didn’t feel like we had much.”
The mechanism is an actuator that fits into open space and controls the throttle according to readings and commands from the rest of the system. It’s a simple concept, but getting it to do what it needs was the key to everything.
“It didn’t fit (in the King Air) because there was a big heavy cable in the way; it was awful,” Hedrick said. “We redesigned the mechanism seven times.”
The same basic technology should work for any plane that has a PT6 engine, and Hedrick said that that list provides a basic roadmap of what platforms IS&S will look to tackle after it finishes with the King Air. But small differences like the cable placement require adjustment. In the end, the company got what it wanted: a small, durable component that can be quickly installed. The actuator takes about 15 minutes to install in a PC-12, and “the King Air is only modestly more difficult,” according to Hedrick.
The autothrottle functionality may be particularly attractive in an aircraft like the King Air or the PC-12 because of intricacies during takeoff and climb.
“For takeoff, there’s a challenge,” Hedrick said. “If you bring the power up too quickly, it will surge the hell out of the engine. In our case, you engage the autopilot by turning it on with a button. In a King Air, it will bring engines up to 700 RPM so you can check levels, then it will bring them up to full power.”
“A single pilot has to keep track of the centerline and monitoring power. It’s not easily done,” he added.
That is specifically for the King Air, of course.
“In a PC-12, there’s a different requirement,” Hedrick said. “There’s a different max torque at different altitudes. It’s good if you have a good memory or want to open the [pilot operating handbook]. But the autothrottle automatically takes care of that — it will fly to the maximum torque, and if you want to adjust to a lower torque, you can.”
There’s also built-in Vmc protection — if a twin-engine plane loses one, it tends to yaw to one side because of the other. There is a vertical stabilizer in place, and ThrustSense calculates where thrust needs to be on the remaining engine to prevent excessive yaw.
In lieu of FADEC, IS&S’s system attaches directly to the engine, allowing the monitoring of thermocouples, torque, turbine speed, which can then be displayed to operators as well as used by the ThrustSense for necessary calculations.
The autothrottle will be available as a standalone installation for $68,000 or as part of a package with the company’s flight deck with displays. Certification is underway for both versions of the technology with the same early-2019 time frame.