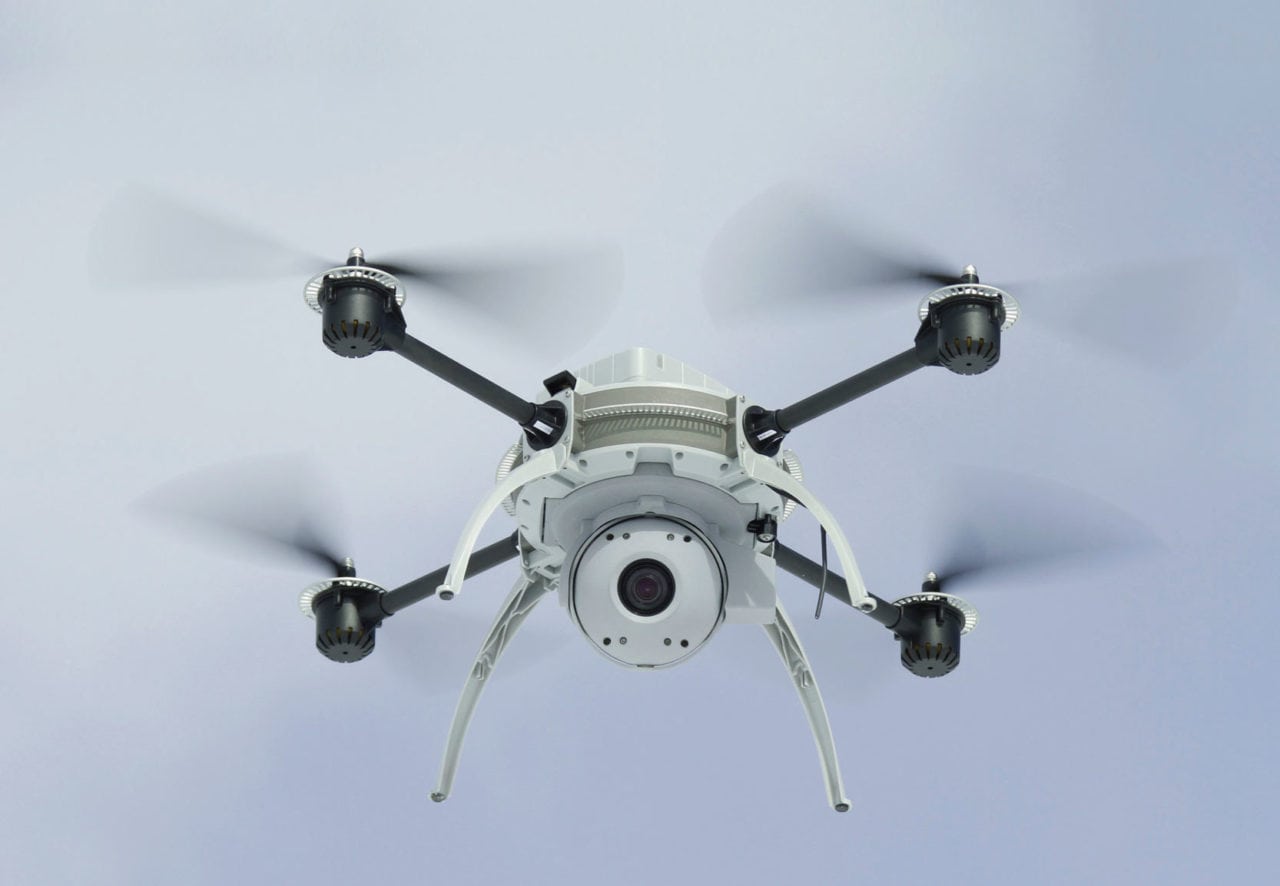 |
The Aeryon Scout micro Unmanned Aircraft System uses an autonomous quad-rotor helicopter to carry quick-change payloads. |
Micro-sized Unmanned Aircraft Systems (UAS) launched by foot soldiers, street cops and industrial users promise real-time information that is both up-close and personal. The Scout micro UAS made by Aeryon Labs in Waterloo, Ontario, has already shown Libyan rebels opposing artillery positions, accident investigators geo-referenced crash scenes and oil refinery maintenance engineers tall flare stacks. The Unmanned Air Vehicle (UAV) can be snapped together at the scene and flown by a non-pilot operator to downlink day video, night thermal imagery and custom sensor data to a tablet ground station more than 3 km (1.9 nm) away. It takes off vertically, follows a programmed flight plan, compensates for winds, calculates remaining battery life and keeps sensors on target automatically. The micro UAS consequently makes big demands on flight control electronics and sensors. According to Aeryon President Dave Kroetsch, “The customer has the same expectations of a micro air vehicle as a larger UAV… You can’t sacrifice performance for size.”
Scout customer ING Engineering in Ottawa, Ontario, is a robotic aviation systems operator with UAVs of different sizes for hire. “We’re a charter aviation company. We fly payloads, not people,” said ING founder and CEO Ian Glenn. “You tell me what shot you want and we’ll try to get that shot for you.” The ING portfolio of platforms now ranges from the 3 lb Scout to the company’s own 49 lb Serenity. ING Engineering used the Aeryon micro air vehicle to collect imagery of the flare stacks for a refinery in Eastern Canada and winter flood zones for the Emergency Measures Organization of New Brunswick province. “One of things I really like about the Scout is it’s easy to use,” observed Glenn. “If your flying task is simple, you can focus on the imagery you’re getting paid to collect, as well as making things safe in your operation.”
 |
Libyan rebels used thermal imagery from a Scout to spot loyalist artillery positions. |
Aeryon began marketing the Scout electrically-powered quad-rotor in 2009, and though the company will not reveal the number of systems sold to date, Kroetsch said his customers are divided evenly among military, government and commercial users. All expect a man-portable UAS to be easy to operate. One Aeryon customer reports the Libyans were able to use the Scout effectively just a couple of days after delivery. “By having a lot of intelligence on board the system, the system is able to manage itself,” said Kroetsch. “The basic flight capability is such that with verbal instruction, you can fly the system in a couple of minutes.” High levels of automation also enable Scout users to concentrate on the information they seek rather than on the platform that provides it. “We tell customers, if at any point they’re focused on the air vehicle, they’ve lost focus on their mission.”
Ride The Wind
The quad-rotor configuration of the Scout offered Aeryon engineers an air vehicle with few moving parts. Four fixed-pitch, variable-speed outrigger rotors enable the autonomous helicopter to take off and land vertically, hover in flight or perch on buildings to stare at targets. “Because the system doesn’t have a front, it can fly in any direction,” noted Kroetsch. “Because it doesn’t have a front, it means we can easily point the camera at the target. You touch the map where you want the camera to look and where you want the Scout to go, and the Scout takes care of the rest.”
 |
An oil refinery in Eastern Canada used color imagery from a Scout UAS to inspect tall stacks without the hazards of climbing or the cost of manned helicopters. |
Most UAS operators at ING Engineering gained extensive UAS experience with the Insitu-Boeing Scan Eagle in Afghanistan. “I also select them from folks who used to sit in the back of AWACS and have a bunch of other aviation skills,” said Glenn. The UAS services company still flies Scan Eagles from Canadian naval frigates and in support of Canadian ground forces, but micro air vehicles including the Prioria Maveric and Aeryon Scout minimize both operator workload and operating cost. “If you want to do something very local — in particular security events — I can put a guy and an aircraft there to support that,” said Glenn. “The larger you go, the larger the logistics.” He added, “I always look at total ownership costs of flying the aircraft.”
ING Engineering initially used Cyber QUAD quad-rotor UAVs made by AT International for select jobs, but Glenn discovered an operating advantage in the Scout. “What I found was the performance of the Scout is much better in wind conditions… When you’re at 220 ft and being blown about trying to image a flare stack, you want as much stability as you can get.”
Compared to bigger fixed- and rotary-winged UAVs, the Scout platform, which is just 31.5 inches across has to overcome special stability challenges. “Ultimately, it comes down to the size and scale from a control point of view,” said Kroetsch. “You’re dealing with winds that are much, much higher proportionally than are experienced by a larger vehicle.” He added, “If you were on one of these little guys, you’d get sick pretty easily.”
The Scout UAS system includes the 3-pound UAV and a ruggedized tablet controller. Payload options include Photo3S for high-resolution still images; VideoZoom10X for 10x optical zoom video; and thermal infrared video.
The gust response of the micro air vehicle impacts both flight controls and stabilized payloads. “You’re getting much more motion out of the platform. That means you have to control faster. That means you get more motion and acceleration from the platform, which puts more demands on the sensors,” Kroetsch said. The Scout changes propeller/rotor speed on each brushless dc motor arm to command pitch, roll, yaw and thrust. “We control the speed of the motors in excess of 600 times a second. We control position as well through that loop.”
Scout top speed is 50 km/h (27 kt), and ceiling about 500 ft for the standard vehicle. Aeryon engineers recently tested new propellers and motors arms at up to 13,000 ft above sea level to enhance micro UAS performance for the high density altitudes like those in Afghanistan. The quad-rotor uses an ultrasonic transducer and pressure altimeter to determine height, and the self-turning control architecture preserved favorable flight characteristics at high test altitudes.
 |
The Scout UAS system includes the 3-pound UAV and a ruggedized tablet controller. Payload options include Photo3S for high-resolution still images; VideoZoom10X for 10x optical zoom video; and thermal infrared video. |
Kroetsch noted that manufacturers of larger platforms can often integrate familiar subsystems to perform common UAS functions. “You can take pieces and parts off the shelf like LEGO, and it works.” In contrast, the micro UAS demands custom solutions. Accelerometer and gyroscopic sensors in full-sized UAVs, for example, can weigh 5 kg to 10 kg. The same sensors in a micro-UAS can weigh no more than 5 g to 10 g. Toaster-size GPS receivers in early UAVs weighed around 3 pounds. The micro UAS equivalent is about 5 g. “There are companies that make all that,” acknowledged Kroetsch, “but when you put all those pieces together, you don’t have the optimization.” He added, “We manufacture essentially everything that goes into the Scout from the ground up… With the micro UAS, you need to design an entire system. Every one of the components in the Scout is designed as part of a system.”
Digital Bits and Pieces
Several critical technologies converged to make the Scout micro UAS possible. The vehicle draws 150W to 200W from a rechargeable lithium polymer battery. “As with any vertical takeoff and landing UAS, you put most of your energy toward keeping the aircraft up,” said Kroetsch. “It’s only really recently that battery technologies are able to put out that type of power.”
Fixed-wing UAVs, including the Maveric naturally provide greater endurance than rotary-wing platforms. “Persistence tends to be the big characteristic,” acknowledged Glenn at ING Engineering. “Some of these have some great flight characteristics… Maveric gives you 15 km range versus 3 [km with the Scout] and more endurance. As a fixed-wing [platform], it has some advantages over a quad-rotor.”
The vertical takeoff Scout flies for only 25 minutes on a battery change but can send imagery to users for up to eight hours from a stationary perch. The quad-rotor avionics architecture packs all vehicle electronics on a single circuit board partitioned to separate flight control and sensor functions. Though Aeryon will not identify Scout processors, separate computers provide real-time flight control response and digital video processing to enhance reliability and simplify testing and qualification. Significantly, the control software calls on the same attitude sensor to control the vehicle and point the payload. The synergy between the two functions ultimately gave the Scout longer flight endurance.
 |
ING Engineering field service representative Kurt Trebels prepares the Scout micro UAS for flight. |
The otherwise purpose-built UAS adopted an off-the-shelf tablet computer ground station made by Xplore Technologies. “We’re relatively platform-agnostic from a software point of view,” Kroetsch said. “We wanted a tablet with ruggedization and a screen viewable over a wide angle at temperatures to +50ÃÅ¡C in bright sun.” The Scout operator uses a tablet stylus to define a flight plan with targets… It’s a little bit different paradigm than a joystick control system,” noted Kroetsch. “They need a pilot with hand-eye coordination. A novice user can fly the Scout in winds up to 50 km/hr (27 kt).”
The Scout concept of operations allows for multiple vehicles to relieve another and keep eyes-on-target when one aircraft battery gets low. The Scout control system also commands a climb and return to launch point if communications with the ground station are lost. The encrypted datalink of the micro-UAS works in the 900 MHz unlicensed IFM — Instantaneous Frequency Modulation — band to avoid regulatory complications and maximize range with a low-power transmitter. The standard 3 km datalink is suitable for most field applications, but range can be extended with special ground antennas. The Scout command tablet can also share digital video with other IP networked devices.
The touch-screen ground station performs a simple red light/green light system check that verifies GPS, accelerometer and gyro performance. The system confirms the vehicle is not moving before a ground launch and provides a moving boat or car initialization routine. It also checks magnetic fields to prevent navigation distortions when launched from large ships.
Quick-Change Payloads
 |
University of Alaska Fairbanks used Scout imagery to create orthomosaic ice maps at the entry to the Nome harbor. The Russian fuel tanker Renda is shown delivering fuel to Nome. |
Annotated imagery from Scouts helped count sea lions in the Aleutian Islands, map the Alaskan coastline and plan assaults on a drug trafficking facility. Aeryon contends sensor imagery from the low-flying Scout rivals that from larger, higher-flying platforms. Imagery collected from 150 ft for a Geographic Information System affords 1 cm resolution per pixel. A manned aircraft or larger UAV forced higher might only provide 10 cm resolution per pixel. Scout image stabilization and precision tracking come from controlling the vehicle position and camera independently through pitch, roll and yaw. An automatic photo-mapping tool enables a user to define a target grid and set the desired level of detail and image overlap. Images are stitched together to create the big picture and shared with other ground stations. “It depends on what the customer wants and needs,” said Glenn. “Usually, we set up so we can share that in real-time with the customer.”
The Scout carries Aeryon’s standard quick-change payloads including the company’s three-axis stabilized color or near-infrared still camera, a 10X optical zoom video camera and a thermal imager based on a commercial uncooled thermal camera core from FLIR Systems. “Nothing in our product is restricted by the U.S. State Department ITAR [International Traffic in Arms Regulations]. We can sell it anywhere,” said Kroetsch. Aeryon also makes custom payloads for different users. A methane and carbon dioxide sensor to register gas leaks and pollution with GPS coordinates was developed for the oil and gas industry in just two weeks. A Light Detection And Ranging (LIDAR) payload for the Scout was sponsored by university researchers. The air vehicle has multiple databuses to enhance reliability and standard payload interfaces to speed integration. ING gives Aeryon feedback on sensors. “We have a very close working relationship. We feed back to all the OEMs we work with what we see as requirements,” said Glenn.
Significantly, ING Engineering uses micro and small-sized UASs with uniform aviation discipline. “The way we do it as not as an ad-hoc organization. We have a Safety Management System in place. The operators I have all have thousands of hours gained in Afghanistan,” Glenn said. The company worked closely with Transport Canada to standardize Special Operating Certificates for UAS operations in regulated airspace. “You’re defining an operation in space and time, the equipment and the people who are going to operate it,” said Glenn. “We now have authority to fly vehicles like the Scout from the Manitoba border east because we’ve proven our ability to Transport Canada with the Scout in a defined set of operations.”
The Scout has meanwhile given Aeryon a versatile micro UAS with broad appeal. “The vision for Scout is to have it in the backpack of every solider and the back seat of every police car,” said Kroetsch. Current industry thrusts are focused on improving the performance of unmanned micro air vehicles. “If we told you it flew for four hours, you’d ask for eight.”
Future improvements may provide more capable control systems. Today’s Scout requires the operator to program flight paths around obstacles; control enhancements may someday enable the vehicle to avoid detected obstacles.
“From a technical point of view, I think the vehicles will become smarter,” concluded Kroetsch. “I think you will see more autonomy in the vehicles. We’re just improving the fundamental specifications of systems today.”