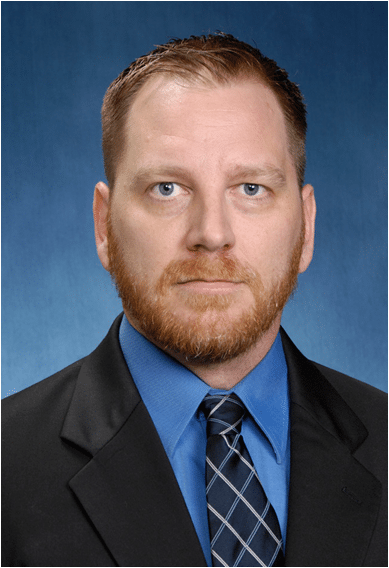
Vitas Mikenas is the chief mechanical engineer for Harris’ F-35 supplier division. Photo courtesy of Harris
In 2017, Lockheed Martin awarded a contract to Harris Corp. to provide the computing infrastructure for new panoramic cockpit displays, advanced memory systems and navigation technology for its fifth-generation fighter jet, the F-35. Under the upgrade, every F-35 will receive new hardware and software to include seven racks per aircraft consisting of 1,500 module components such as new antennas and weapons release systems.
The Florida-based manufacturer confirmed in April 2018 it had completed the delivery of more than 1 million F-35 avionics components to Lockheed. Avionics caught up with Vitas Mikenas, the chief mechanical engineer for the F-35 supplier program at Harris to learn what it’s like to lead the mechanical side of the most electronically advanced fighter jet in the world.
Describe your career and educational background and how it led to your current position as an engineer with Harris.
I did three internships with Harris. After graduating I joined Harris full time, so I’ve been there for 18 years now, first started working with a lot of diverse different things, so around satcom areas, reflector jobs, in addition to some of our wireless products groups doing some mechanical packaging there doing some analysis.
After that I got the assignment to join JSF in an early design phase, it started out as a three month project, and I became an IPT lead for one of our rack assemblies and took over more responsibility and evolved into becoming the chief mechanical engineer for all the rack and modules that we’ve done. So I got involved very early on in the program for what we call the JSF, I got to see the draw up of the design and the requirements and how that all came together and now transitioning into one of the biggest production jobs Harris has ever seen. It’s cool to see the whole spectrum of the engineering lifecycle.
Just recently we’ve had a few tech refreshes with new technology coming on board — higher speed, higher capacity technology for the F-35 that we’ve designed back into the system. Some of our rack assemblies have been intermixed with our work as well.
What does your job require of you on a typical day?
One of the things that keeps me engrained and excited about the work is that it’s a new adventure every week. For the most part, my job revolves around three different areas. The first one is customer support. What that entails is evaluation of damaged hardware, potential noncompliant hardware or some sort of performance issue that popped up at the assembly line out at Lockheed or even supporting some things out in the field, at U.S. Air Force bases, a lot of problem-solving, root cause for corrective action type stuff. The second piece is internally: in-house support. We do a lot of assembly at our Malabar site in Florida. There’s a lot of support there on assembly issues. The third is supplier support and working with suppliers through quality assurance, trying to build a zero-defect-type culture.
We try to predict what their quality issues are going to be and put measures in place to prevent those. The other thing we focus on is capacity. One of the big challenges on the production side of the job is ramp rates, and making sure our suppliers can support that ramp rate and eliminating bottlenecks, keeping costs down at the same time.

A chart providing examples of Harris-supplied F-35 components. (Image courtesy of Harris)
Harris plays a big part in delivering components to every F-35. What are some challenges the company faces in ensuring the proper functionality of each component?
That ramp rate while meeting the cost and affordability goals. The ramp rate is coming; we see it, and the biggest challenge is the focus on quality, ensuring quality and maintaining the hardware tactical baseline that we established in the design phase. The challenge also is getting parts in on time, being 100% compliant. The cost of the aircraft needs to come down. Our zero-defect culture and capacity analysis help to support that.
How is the engineering work you’re involved in advancing and evolving the CNS or any other operational capabilities associated with military aircraft such as the F-35?
From my perspective, it’s the desire for increased data rates and processing capabilities. How that flows into my world of mechanical engineering is how are you going to package these electronics that are getting bigger and hotter. How are we going to deal with the electronic packaging issues that are coming down the road and also the thermal management techniques that are being employed? Some of the traditional thermal management techniques we’ve used in the past aren’t necessarily going to work with the data rates we’re going to see in the future.
One of the unique things we do is we use an APG. It’s actually a graphite embedded into an aluminum heat sink that really helps thermal dissipation, so we’re on the forefront of using that technology. Looking for what’s going to be the next advancement in engineering and thermal management is going to help us down the road.
Electrical engineers like to pack as much as they can in there to get that processing capability, and we’re stuck with figuring out how we can meet our requirements from a thermal management and capacity and vibration view because things are getting heavier and hotter, so that’s going to be an issue going forward.
When you look toward the future of military avionics functionality, what do you expect that is not available today?
Keeping up with that desire for increased processing capabilities and the resulting impact on mechanical packaging and thermal management — so we have to keep looking to meet the solutions out there.