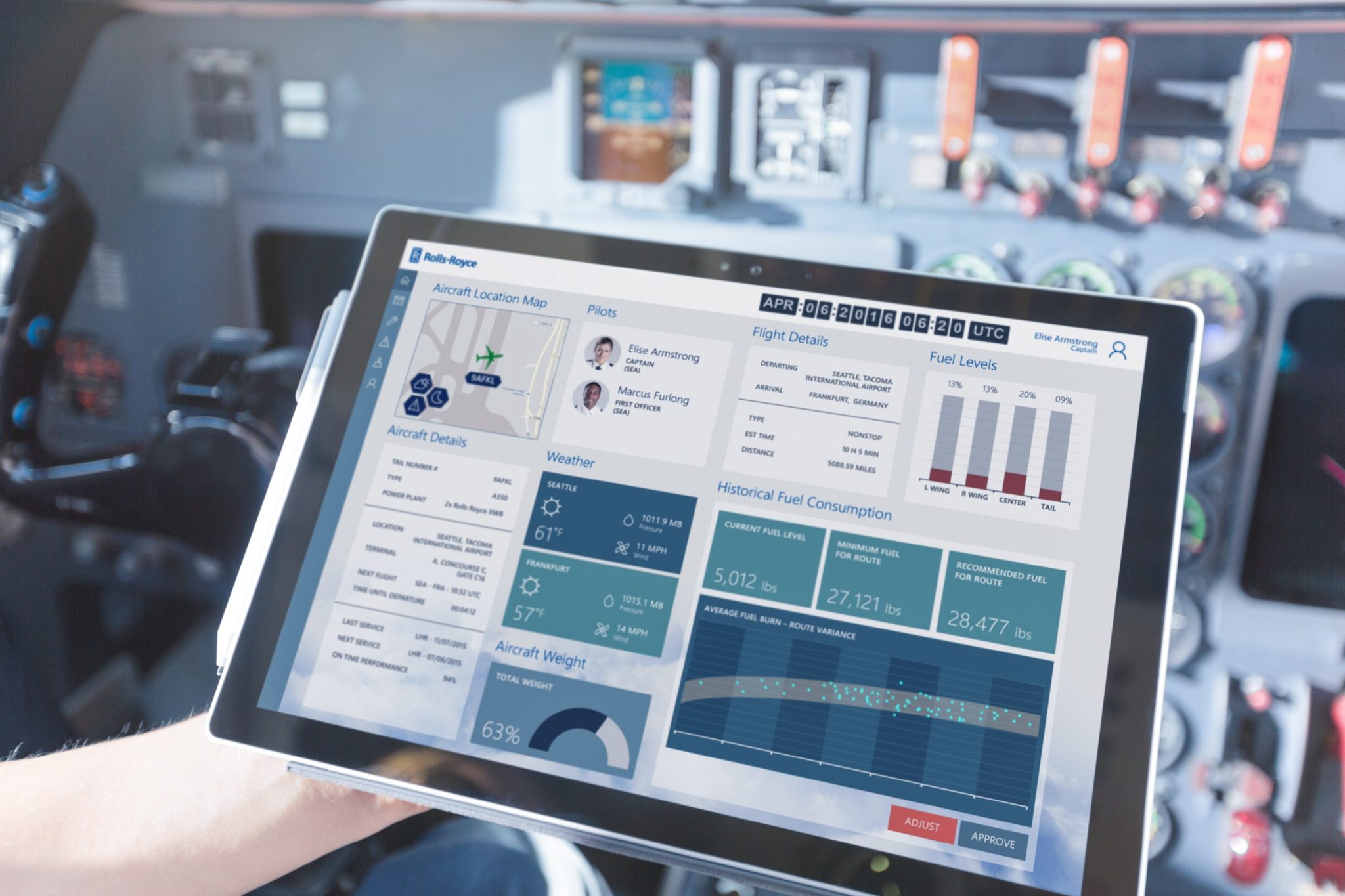
Rolls-Royce is using Microsoft’s Azure cloud-based services for information gathering and storage.
Aircraft engine original equipment manufacturers (OEMs) are introducing cloud computing, embracing the Internet of Things (IOT) and using new data-acquisition technologies to improve the way engines are monitored and maintained.
Using a range of smart data analysis, predictive tools and engineering expertise to add additional insight, engine OEMs are helping airlines reduce fuel usage, fly routes more efficiently, and ensure the right teams and equipment are in place to service engines more quickly and to maintain the highest levels of availability. By improving the way engine health monitoring data is collected and analyzed, OEMs can maximize the operational life of engines and also help operators become more predictive and less reactive in terms of repairing and replacing their aircraft engines.
Historically, engine data has been compressed onboard the aircraft into small reports about how the engine is performing at takeoff, climb and cruise. Now, with wider bandwidth and increasingly connected aircraft, the OEMs are able to access data recorded on more parameters almost every second. This has allowed them to improve the aftermarket health monitoring services they can provide for their customers.
One of the ways engine OEMs are improving their data collection methods is through partnerships with both traditional and nontraditional aviation companies. As an example, collaborating with Microsoft is Rolls-Royce, whose engine heath monitoring service currently monitors 13,000 engines in service on approximately 9,000 commercial flights per day. Under a partnership first announced at the 2016 Farnborough Airshow, Rolls-Royce is using Microsoft’s Azure cloud platform and Azure IOT suite to collect and aggregate data from disparate, geographically distributed sources and Cortana Intelligence Suite to uncover data insights.
“IOT is an important technology. For Rolls-Royce, it can mean connected machines in the manufacturing process, and it can mean connected engines,” Bill O’Sullivan, Rolls-Royce’s communications manager for civil aerospace communications, told Avionics. “Modern aircraft can provide a wireless channel to update elements of the engine monitoring unit. Looking forward, this is likely to increase, with a greater degree of connectivity and agility in tuning the engine data capture and on-board analysis to respond to different operating environments.”
Rolls-Royce also announced a selection of SITAOnAir’s Aircom FlightMessenger to receive and distribute the thousands of data messages generated by its engines everyday. The Aircom FlightMessenger is hosted on SITA’s AirTransport Industry Cloud platform, which is connected to 380 airports, 17,000 air transport sites and 15,000 commercial aircraft.
While the majority of aircraft engine health monitoring capabilities have historically been associated with new-generation aircraft, the trend of more airlines equipping their aircraft with 3G transmission capabilities has also enabled more offloading of data.
Elsewhere, GE Aviation recently announced partnerships with Avionica to bring real-time engine prognostic capabilities to its CF34-3 engines.
According to Tom Hoferer, GE Aviation’s general manager of business and general aviation of commercial support and services, the partnership will bring Avionica’s quick access recorder (QAR) technology to the Bombardier Challenger 600-series aircraft.
“Currently on the CF 34-3, the only way to get the diagnostic data we need is stick a flash drive into the engine data computer and download a nasty text file and send it to a computer and email it to an inbox at GE,” Hoferer told Avionics. “We really see this as an opportunity to bring some digital life into an older aircraft and use some of that continuous engine operation data.”
Another reason GE chose Avionica for that particular partnership was due to the adaptability of its QAR, as data communications methods and protocols evolve, there would be just a slight upgrade to the small QAR box. Therefore “we’re not going to have an obsolete 4G QAR here or whatever, as the cellular technology changes, the product is adaptable,” says Chad Harris, aftermarket services and customer support leader for business and general aviation at GE Aviation. The company expects to make its prognostic health management service available to the 200 CF34-3 operators in more than 70 countries this year.
Furthermore, the use of new data acquisition technology is enabling engine OEMs to track temperatures, pressures, multiple types of low-end and high-end rotor speeds and vibration across full-flight profiles. Over the last year, Pratt & Whitney has been doing this by expanding the capabilities of its Advanced Diagnostics and Engine Management system, which is a suite of algorithms and web tools that customers can access via our customer portal.
On the Geared Turbofan (GTF) engine, which first entered service last year, the OEM has expanded the number of reports that it’s able to get off the aircraft by about three times as much as before, Lynn Fraga, Pratt & Whitney’s manager of business analytics and engine services, told Avionics.
Fraga says Pratt is currently exploring IOT concepts that will help improve its engine connectivity diagnostics and prognostics capabilities. She believes the next generation of engine health monitoring will stem from the use of more enhanced flight data acquisition storage and transmission technologies.
“We’re currently working on our eFAST (enhanced flight data acquisition storage and transmission) next-generation technology, which is designed for the large commercial engine market,” says Fraga. “In 2017 we’re working a trial program to expand eFAST to obtain an FAA supplemental type certificate, which we expect to achieve this year.”