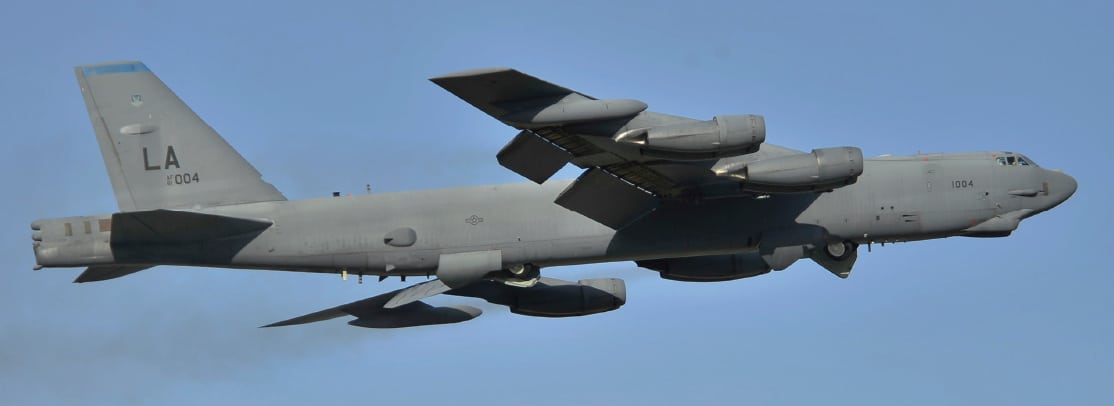 |
A B-52H Stratofortress takes off from Eielson Air Force Base, Alaska, in 2009. |
The U.S. Air Force’s aging airplanes need careful tending — especially their airframes and engines. But the avionics systems in this age of mass-market electronics are often a headache as well. Obsolescence is far more common today than in the days of mil-spec. And even the newest upgrades face these issues before they are fielded. But the military has adapted and now wields a number of weapons. While these can’t defeat obsolescence, they make it manageable.
There are two kinds of obsolescence — material and operational. Material obsolescence is a fact of life in the commercial off-the-shelf (COTS) era. Although this can affect whole configurations of aircraft, it does not drive major upgrades. Those are prompted by the threat of operational obsolescence. Because of budget constraints, program offices often can’t afford regular component refreshes. Instead, they study data from many sources and let this information — and analysis based on it — guide the initiation of component upgrades.
“COTS is a two-edged sword,” says Gary Hebert, deputy system program manager in the A-10 System Program Office (SPO). “It brings capability, opportunity and flexibility, but it’s a fast-moving train.” What’s produced today probably won’t be around next year. It’s almost like buying a cell phone which is obsolete at the moment of purchase.
“You need to remain agile,” he says. When you’re building a product, you need to look not only at the lifecycles of its components but at the vendors’ roadmaps for the component families.
Nevertheless, “when it comes to avionics, the ‘O-word’ doesn’t scare me as much as it used to because we’ve got some ways of predicting what’s going to happen,” Hebert says, alluding to tools like parts databases and predictive analysis. More importantly, he says, the service has the capability of replacing hardware functions with chips such as field programmable gate arrays (FPGA) and programmable logic arrays (PLA).
“In the defense market, while platforms may age, we are going to see a lot refreshes in terms of comm gear, nav gear, displays and other avionics products,” said Bob Smith, chief technology officer at Honeywell Aerospace at the Avionics for NextGen conference in September.
B-52
When it comes to obsolescence issues, the image of the B-52 rises in one’s mind. The youngest Stratofortress is 50 years old and these aircraft are expected to fly through 2040.
There are 76 B-52Hs still flying, out of 744 that were built, says Col. John Fisher, B-52 system program manager. The SPO uses both bottom-up and top-down tools to monitor parts obsolescence. Like other Air Force SPOs, it relies in part on the Air Force Sustainment Center and the Defense Logistics Agency for assistance.
 |
An A-10 Thunderbolt II moves to take position off the right wing of a KC-135R Stratotanker, after refueling mid-air during a training flight over Michigan in July. |
But the SPO also has “very active integrity programs to manage structural, mechanical and avionics systems integrity on the B-52,” says Jerold Smith, chief engineer. Integrity programs look at reliability indicators, failure mode data and usage data. They are set up to examine system and component design and anticipated lifecycles, and then to perform predictive analysis in order to plan maintenance, repair and overhaul. The programs also involve evaluations in the field and depots to see if wear is occurring as analytically predicted, Jerold Smith says. If there is a negative difference between what the predictions are and what the aircraft tells you, “that tells us we need to take some preventative action or do some tech refresh,” whether on a structural member or an avionics component, Jerold Smith explains. The refresh program would be put in place before the item failed.
The SPO also tracks all the boxes and components on the aircraft against maintenance man-hours, Jerold Smith says. “We can see where the maintenance man-hours are expended,” and then, based on that information, “we can target improvement initiatives to try to reduce that workload.” It is a methodology to discover — and solve or improve — both component and maintenance issues.
This attention pays off. The B-52 fleet is two aircraft over the Air Force’s availability requirement, says Wendy Walden, chief of the SPO’s Logistics Branch.
 |
B-52’s CONECT program replaces monochrome 8×10-inch multifunction displays (MFD) at all five crew stations with full-color 8×10-inch MFDs that increase situational awareness by creating a “common sight picture.” |
CONECT
The B-52’s biggest ongoing avionics upgrade is CONECT, or Combat Network Communications Technology. CONECT replaces monochrome 8×10-inch multifunction displays (MFD) at all five crew stations with full-color 8×10-inch MFDs that increase situational awareness by creating a “common sight picture,” if required; it adds a 1-Gigabit Ethernet digital backbone, so that boxes can share data more quickly; it adds data links for retasking aircraft and retargeting weapons while the B-52s are in flight — something that is not possible today; and it installs a digital interphone to aid communications between crew members.
Although CONECT will solve some obsolescence and reliability issues, the upgrade was driven by the threat of operational obsolescence. “We have to make sure that we’re tied into, not just the U.S. Air Force, but the joint force,” Fisher says, with network-centric capability, for example.
CONECT has been percolating since 2005, and the first “kit proof” will be installed on an operational aircraft next year, at the beginning of low-rate initial production.
Not surprisingly, CONECT has already experienced obsolescence issues. The team has identified some potential items and is putting strategies, such as life-of-type buys, in place, Walden says.
So far the program has made three or four end-of-life buys, some of which involved numerous parts, says Scot Oathout, director of B-52 programs, Boeing Defense, Space and Security. It reports monthly to the procurement office on obsolescence monitoring. The program also subscribes to a “fairly universal commercial [part tracking] service” and has agreements with its major suppliers “to periodically monitor the supply base.”
More importantly, however, CONECT’s architecture is designed to make the non-hardened computational segments easily upgradeable, says Jim Kroening, Boeing’s B-52 development program manager. “We use standard interfaces and can essentially drop in a new board.”
The hardened components required for nuclear missions are much less volatile and subject to technology evolution.
A-10
The A-10 tank-killer is also out of production — the last plane was delivered 28 years ago — yet the fleet is expected to fly till as late as 2040. Although the aging airframe presents the biggest headaches, avionics sustainment is also a challenge.
While the SPO relies on the Sustainment Center, it is taking additional steps to improve early warning. It conducts studies that may catch issues not flagged in the parts databases, Hebert says. A system-level study may be prompted, for example, by reports of problems in several related boxes, explains Jerry Coates, the SPO’s operational safety, suitability and effectiveness integrator.
The SPO is also preparing an A-10 Platform Obsolescence Plan. The winning contractor will load the A-10 bill of materials into the commercial Advanced Component Obsolescence Management (AVCOM) database and focus solely on the A-10’s needs.
The program office also notes the importance of test equipment support. Over the last three years the SPO has worked with experts at the Warner Robins Air Logistics Complex to develop a Support Equipment Road Map. This software tool, populated with 18,000 elements of A-10 support equipment, allows managers to highlight reliability, supportability and obsolescence issues. The effort also involved organic development of the portable automated test set (PATS-70), a unit that tests a lot of avionics.
F-16
The U.S. Air Force currently operates about 1,000 F-16s, about one-third of the worldwide fleet. The F-16 is more fortunate than the B-52 and the A-10 in having an active production line to help with spares.
The F-16 SPO teams with the Sustainment Center, which focuses on scanning parts databases for obsolescence issues, says Col. Mark Mol, F-16 system program manager. “Their goal is to maximize the effectiveness and efficiency of the supply chain, and my goal is to ensure the safety and suitability of the fleet.”
However, there are often synergies between the two perspectives. Take the fire control computer upgrade. The prior system was based on long-outdated computing technology with limited memory capacity and data throughput and limited spare parts availability, explains Mark Greenamyer, the SPO’s avionics program manager.
The SPO looked at what could be done at the chip, card and box level, but it made more sense to replace the mil-spec system with one based on ruggedized commercial technology — the Commercial Fire Control Computer. The processing power and memory improvement that came with the new system made it “a much cheaper approach than solving individual [obsolescence] issues,” Greenamyer says.
The SPO does not have regular refresh intervals, Mol explains, as this “would require an extraordinary amount of funds to address potential problems that may not actually materialize.”
The SPO also receives reports on the “total non-mission-capable rate” for supply or maintenance, Mol says. “So when we identify a negative trend, we’ll start doing root cause analysis” to track down the source and develop a solution. This process can turn up issues such as obsolescence, repair process problems, technical data problems, contract issues or even operational issues.
The last resort for the SPOs is the “boneyard” at Davis Monthan Air Force Base in Arizona. But supplies there are limited and, although the aircraft have been protected from the elements, the condition of their avionics systems is unknown and components such as commercial chips and boards would probably be obsolete. (Davis Monthan is a more likely source of components such as antenna bracketry.) “We also would need to run [components] through additional tests to ensure that they meet airworthiness criteria,” Mol says.
The “O-word” is still scary Mol says. “We know we can overcome the challenges, but … it takes considerable budget to address.” An obsolescence issue is typically not a question of one or two or three components, he says. You might be able to get those from the boneyard. A true obsolescence issue could affect an entire configuration of airplanes — it’s a big issue to solve. “Only when I do a lifetime buy or redesign” do I solve it.