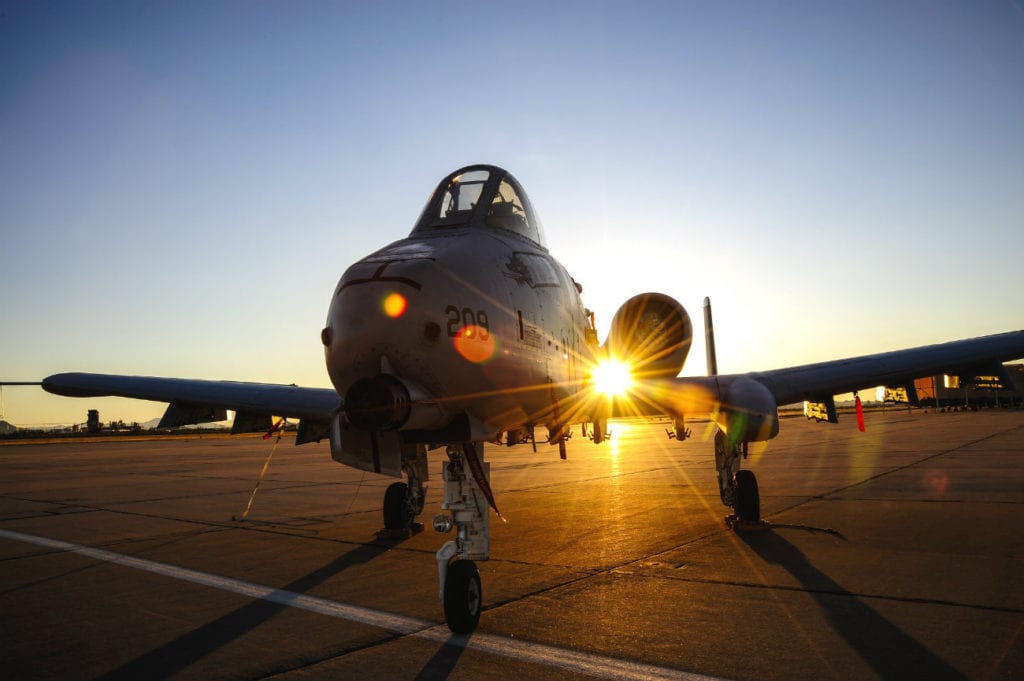
In service since the late 1970’s, the A10 Thunderbolt is still a vital aircraft of the U.S. Air Force defense strategy. Supporting legacy sustainment by providing extended life-cycle repairs for the POWERCORE VME-695 and POWERCORE-6604E embedded boards originally by Force Computers for L3. Obsolescence issues faced by commercial and military operators are a major challenge that the embedded systems supply chain is still grappling with when it comes to avionics upgrades, replacements and repairs. Photo: Staff Sgt. Angela Ruiz, U.S. Air Force.
Product obsolescence is not new to aviation, and neither are the costs and inefficiencies caused by this issue. Yet some industry experts say too often, the avionics industry fails to take a strategic view on how to manage obsolescence as a business process.
“We need to stop treating obsolescence like an exception; it’s a fact of life,” Ethan Plotkin, CEO of GDCA, Inc., told Avionics International. “We need to shift obsolescence from this big crisis and scramble to just another manageable business process.”
Speaking to OEM suppliers at the Embedded Tech Trends forum in Atlanta this past January, Plotkin noted that across industries companies are spending too many resources trying to address the market challenge of older, obsolete products. He cited the 80/20 principle that his company finds that 80 percent of revenue comes from 20 percent of a company’s SKUs while only 20 percent of net profit goes toward obsolescence issues.

Ethan Plotkin, pictured here giving a presentation during the 2020 Embedded Tech Trends event in January, is the CEO of GDCA, a certified FAA Repair Station that repairs and manufactures boards plagued by obsolescence issues and offers a broad range of solution options for sustaining long lasting aerospace and defense equipment.
In 2018, airlines spent $75.9 billion on maintenance, repair and operations for their products while obsolete or damaged spares cost airlines over $3.6 billion, according to Frost & Sullivan’s 2019 report, Navigating through Operational Turbulence.
Dayton, Ohio-based product support solutions provider ONEIL & Associates helps aerospace, commercial, and DoD customers maximize the life of their equipment using big data analytics to analyze and predict parts breakdowns proactively. The company’s technology used in commercial aerospace is being evaluated by the Air Force as part of the DoD’s SBIR program.
Bruce Joiner, director of business development for U.S. Air Force at ONEIL & Associates has witnessed the obsolescence issues that defense acquisition officials have had to deal with in recent years.
“Maintaining legacy systems is a big problem within the Air Force and across the DoD. The original OEMs may have the tooling for a lot of those components, but they are no longer in the business of producing them. We see these impacts in the commercial aerospace sector as well,” Joiner said.
In Joiner’s experience there is never a diminishing parts issue until there is a failure, “the higher rate of failure, the faster or more intense the diminishing parts issues are revealed,” he said.
“The best way aviation companies can manage this challenge is to shift their expectations from crisis management to a solution for sustainment,” Plotkins said, noting that companies can re-think how they go about planning for demand of aging product lines. A typical practice to offer a “last time buy of obsolete components” is not a long-term solution.
One thing is clear: the need for aftermarket parts in aerospace is not going away. The global commercial aircraft aftermarket parts market size is estimated to reach over $51 billion by 2026, according to Market Study Report’s latest study on this issue. Plotkin notes that “a large percentage of that $50 billion is and will continue to be obsolete electronics.”
GDCA, which provides proactive obsolescence management for embedded computers, is hearing more from aviation customers, especially in defense, of the struggles to keep up with the fast pace of electronics obsolescence, especially in large procurements. Many companies aren’t aware of third-party legacy manufacturers such as GDCA, ES Components, xsmicro and eComp.
Using Predictive Analytics to Get in Front of Obsolescence
Upgrading and recertifying avionics equipment is a costly proposition. ONEIL’s Joiner agrees, which is why the Air Force and other military branches are beginning to use AI to predict when parts may need to be replaced and to plan ahead using service life management solutions. The company uses condition-based maintenance analytics to allow them to look down range and give them and suppliers lead time to respond to aging electronics and other parts caused by vibration, corrosion and other contributing factors.
“The DoD manages legacy systems that have been in use well beyond their lifecycle. Airframe components and system component failure is just a natural part of the aging process,” notes Joiner, citing the B-52, C-130 and the F-15 as examples of aircraft that continue to be maintained for multiple decades beyond their intended life.

Staff Sgt. Jason Hurst references a technical order while inspecting a C-17 Globemaster III engine April 15, 2011, during a biannual home station check at March Air Reserve Base, Calif. Sergeant Hurst is a crew chief assigned to the Air Force Reserve Command’s 452nd Maintenance Squadron. Photo: U.S. Air Force/Val Gempis
Plotkin said component issues can occur in defense, medical, and transportation applications while a system is still in design phase. Without the original COTS IP, such programs face critical downtime, redesign and recertification.
Even as the aviation sector relies on COTS components and feels the effects of the fast pace of processor and component obsolescence, awareness of real options to tackle obsolescence in a sustainable way eludes many companies.
Obsolescence Pushing Some to Return to In-house Development
One troubling trend he’s noted is companies not liking that they can’t own their own Intellectual Property (IP), rejecting commercial-off-the-shelf (COTS) components right out of the gate in favor of building their own electronics in-house. Plotkin says turning away from COTS – technology that allowed industries to get to market faster and cheaper while focusing on what they do best – is the wrong approach.
“You can build airplanes; you can build computers. I’m not sure you want to try to build both,” he cautions.
Plotkin said he’s seen the pendulum swing toward in-house engineering within both medical device and semiconductor manufacturing but that the same component obsolescence issues remain. “They have armies of electronics engineers who have control over the design but they find it is harder for them to sustain those products than it was for commercial COTS OEMs,” he says.
Companies often will invest significantly in pre-stocking components for future needs, which creates another problem.

Navy Used GDCA for Seahawk Helicopter Circuit Card Assembly
As a legacy equipment manufacturer that proactively manages obsolescence in embedded computers, GDCA has helped the aviation sector address the challenge of early part and component obsolescence. For example, it consulted with the U.S. Navy when the MH-60 Seahawk helicopter procurement stalled because of a shortage of a critical circuit card assembly that controlled a weapon system on the aircraft.
“The primes were putting pressure on the board OEM supplier to build another batch of boards. Despite some heroic efforts, the obsolescence in the design meant they couldn’t feasibly build enough to meet the demand. This meant the Navy was facing $5M to $10M in non-recurring engineering costs to upgrade the entire system, which didn’t make sense. Instead, the OEM transferred the technology to us and we were able to solve the obsolescence issue, re-start the production line and crank out the order to the Navy to get them through the acquisition,” recalls Plotkin.
Experts agree that the entire supply chain serving aerospace across the commercial and defense sectors will need to embrace proactive solutions if they hope to manage the continual challenge of product obsolescence.
“We owe it to our suppliers and system owners to provide as much lead time and information as possible for them to design products that are built with longevity, quality and technology in mind for today’s environment,” concludes Joiner.